Disclaimer: As an Amazon affiliate, I may earn a small percentage from qualifying purchases. This is at no extra cost to you. Learn more here.
Last Updated on January 10, 2024 by Larry Edwards
It’s okay to be skeptical when going for a metal lathe. You need to scrutinize every feature and spec, so you don’t end up buying a lathe that is not worth investing in.
So, when you are looking to invest in a new metal lathe, whether it’s small or professional, consider the following:
- What size do you need?
- How much power does it have?
- Is the machine durable and robust enough to withstand heavy loads, or is it more suited for lighter jobs only?
- Do I want a belt pulley or variable control?
- The quality of the built-in quick change tool post
- Warranty duration and customer support.
If these questions are confusing, don’t worry. I will help remove some of that mystery! So do read through before deciding anything or purchase any product related to metal lathes.
Why are lathes so expensive?
There are reasons for this machine to be expensive because of its complex engineering. Lathes are tools that can create more complex machinery and metal parts, especially for industrial purposes.
You might have heard that it is called the mother of all machines.
A lathe machine is made up of many moving parts that have to work together in perfect unison so that the final product has no defects or wobbling bits stuck on it.
This includes all types of shapes like cubes and spheres and difficult shapes such as cones and cylinders. The precision required for this kind of machinery means that they’re not only expensive but tough to build too!
But anyways,
- A lot depends on what type of project you want to do with the machine: where precision is needed.
- You can buy cheaper ones and fix them up by replacing parts that wear down over time (such as bearings) – this way, you save money in the long run! You might even get lucky enough to find one on Craiglist, eBay, or Facebook marketplace.
- Don’t buy something too expensive that your repairing cost might become more than replacing it altogether.
- I would not recommend going below 700 dollars while going for a mini lathe. I am talking about a brand new one.
Metal lathe checklists for buyers
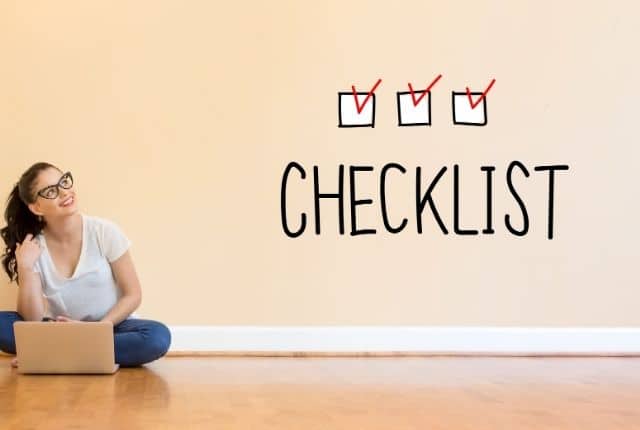
To me, buying a metal lathe is always a great investment. So, whenever the need arises to opt for a machine, I start thinking of this as a stock investment.
Now, the cost of a new conditioned mini Lathe starts from $600 to $700 on average, whereas a used one will be less expensive. But it’s often hard to find the quality because of the lack of expertise.
It becomes more difficult if you’re looking for something specific like a bench-top size or variable speeds on a used or old one as they are already underpowered as new.
So, I always suggest new turners to go for a brand new one under the range.
Let’s go and see some of the must-check things before you buy any lathe.
1. What size metal lathe should I buy?
This is the most typical yet important question for a newbie. What size to get?
To give you an easy answer, I would say that it depends on the size of the project you are willing to work on.
If you tend to do something like yo-yos, pens, small steel/aluminum ornaments, and small stuff, you can use any mini metal lathe of about 6 x 12 or 7x 14 inches in diameter.
If your work is larger than this, you need to think bigger.
I would say go for something that can grow with your skill. Don’t buy tiny machines to save money. You might have to sell it with a low resale value when upgrading.
2. Price according to size, power, and torque range
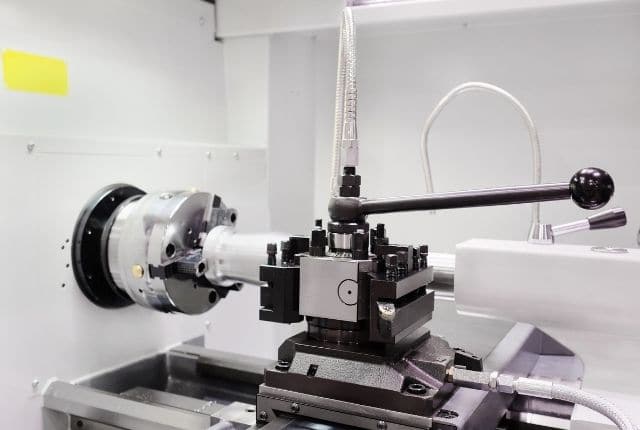
This can range from small benchtop machines with less than 0.5 HP up to large industrial units with over 800 HP worth of torque. The width of its bed should be at least 14-18 inches wide. I would not go below 7″ swing.
The price also varies greatly based on this feature alone; smaller models typically cost $500-$1000 while larger ones will cost you upwards of $30,000.
This will depend on what you want to make with your lathe machine. For light tasks that require less than 2 HP worth of torque or undercutting/threading applications, a smaller benchtop unit should suffice.
If you plan on working in metals like stainless steel alloys (300 series), aluminum alloys (1100-1300 series) or workpiece weights over 160 lbs., then a larger model would be more appropriate for those heavy-duty jobs.
3. Another important feature is durability
Larger machines are typically sturdier and made from thicker material which can minimize wear and tear but also adds weight–something to keep in mind. But not everyone can afford one.
Whereas, benchtop lathes are compact in size and weight that is suitable for small or home workshops, which can offer a convenient and inexpensive alternative to those who don’t have space for a large machine.
Try to feel how if the controls are easy to navigate. Check if there are any extra features like any led light or laser guide that you want.
Go for the lathe that comes with a 3-jaw chuck. Buy something with variable speeds so you can work on both finer details as well as heavy-duty projects.
This will make your life easier in many ways!
4. The size of your projects also impacts
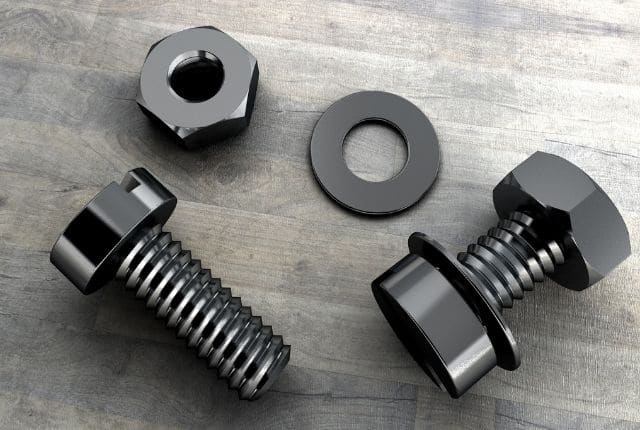
If you often work with smaller pieces that are under 12″ in diameter, then it’s more cost-effective to purchase a benchtop model versus one that is too big for small-scale projects.
A heavy-duty metal lathe might be out of budget and not worth the investment for home shop.
5. Manual belt-driven or variable speed lathe?
There are two types of lathes: manual belt driven and variable speed. Manual machines have speed and direction features that you control by hand with levers or buttons on the front panel. They’re slower to work with but also cheaper to buy.
On the other hand, variable-speed models operate at greater speeds when precision is more important than cost-effectiveness. You control the speed with a knob without stopping the lathe.
So, it’s important to evaluate your needs and budget before deciding which type of lathe you should purchase.
6. Warranty and customer service
See what kind of warranty they offer when buying from an online retailer because this will also tell you about customer service quality.
In other words, go for well-known brands.
7. What tools do you need besides the lathe?
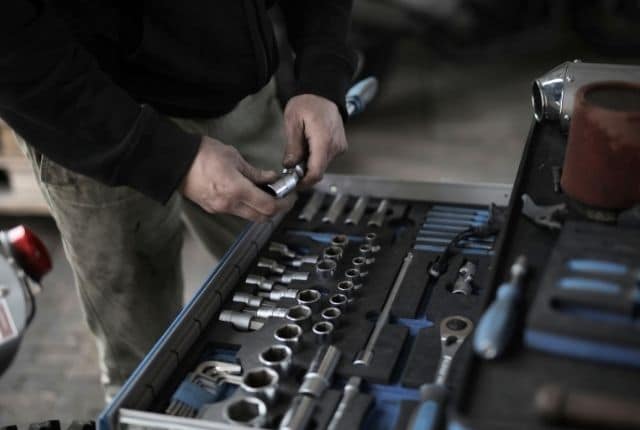
Always remember that a lathe is not the last thing you need. You need different kinds of cutting tools besides the lathe.
Now, what tools you are going to need depends on what cutting process you are performing. Like-
- Turning tool
- Boring Bar
- Chamfering tool
- Facing tool
- Parting tool
- Grooving tool
- Thread cutting tool
You can also read my article here to understand the cutting tools deeply.
8. Can I sell my metal lathe with a good resale value?
There comes a time when we think of upgrading our current lathe with a bigger and upgraded one. And most of the time we sell our used one to buy the new one.
So, if you’re looking to sell your metal lathe, I recommend trying eBay and other auction sites. You may run ads on the Facebook marketplace and get a lead.
You could also try posting on local classifieds pages in your area or even selling it in person if any shop deals with second-hand machinery nearby.
Recommended brands for hobbyists
As I already have a comprehensive guide written on the best mini metal lathes, I will link it down so you can read that separately.
Check my guide on the best mini metal lathes that every hobbyist should know.
Please let me know in the comment what you think. What your process of inspecting a lathe before purchasing?