Disclaimer: As an Amazon affiliate, I may earn a small percentage from qualifying purchases. This is at no extra cost to you. Learn more here.
Last Updated on February 28, 2023 by Charles Wilson
Face milling and peripheral milling operations are two terms you might encounter when dealing with the different machining processes.
While both aim to remove material from a workpiece with a rotating milling cutter, face milling and peripheral milling still have KEY DIFFERENCES, specifically in how they perform their tasks.
But what is the difference between face milling and peripheral milling operations?
I’ll answer your question bit by bit as I closely compare face milling vs. peripheral milling in this article.
Key Takeaways:
- Face milling and peripheral milling are the two primary types of milling operations.
- The two machining processes mainly differ in purpose, directions followed, correct positioning, and other factors.
- The MAIN GOAL of a face milling operation is to create a smooth or textured surface finish on the workpiece and remove just a minimal amount. It primarily uses face mills in its operations, but end mills can also be used.
- Peripheral milling likely involves machining a flat or formed surface and removing large amounts of material. Instead of a face mill, a shell or end mill is used.
What is Face Milling?
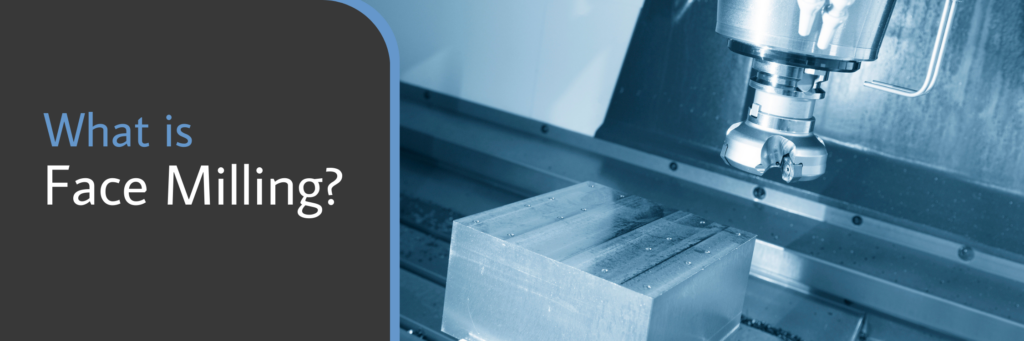
Face milling operations are a machining process where the milling cutter is positioned parallel to the workpiece. This is because the process aims to grind the sides of the cutter on the surface of the workpiece.
In face milling, the rotating axis of the cutter is positioned perpendicularly on the surface machined to achieve a FLAT and SMOOTH top face.
When face milling, I highly suggest using milling cutters designed for facing, such as fly cutters and shell mills. But if you’re aiming for a different finish, an end mill will help significantly.
Generally, face milling involves general face milling, high face milling, heavy-duty face milling, and finishing with wiper inserts.
How Does Face Milling Work?
Once the face milling process has begun, and the spindle starts spinning, feed the face mill on top of the workpiece. In this phase, you’ll be using the end of the cutting tool for material removal.
The teeth on the milling cutter will distribute the chip load, while the teeth of the cutter on the periphery completes the cutting job.
The feed rate of the face mill is HIGHLY DETERMINED by the number of teeth on the cutting tool, material of the workpiece, the depth of the cut, rigidity of the tool, and force applied by the vise or fixture.
NOTE: Make sure that the machine spindle, which holds the cutting tool, is rotating at the right RPM (revolutions per minute).
What is Peripheral Milling?
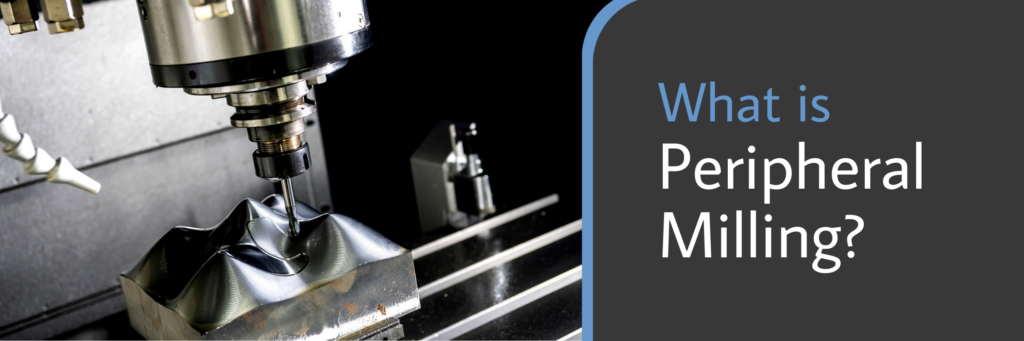
Peripheral milling operations involve using an end mill or shell mill, even if the removal of material from a workpiece mainly happens on the sides of the cutting tool.
An end mill and shell mill looks similar to a drill bit with a flat tip.
In peripheral milling, end mills remove material from a workpiece at the periphery during the machining process, unlike face mills that remove material at the top to produce flat surfaces.
How Does Peripheral Milling Work?
A peripheral milling operation also constitutes end milling. Before feeding the tool into and around the workpiece, it should first be positioned at a predetermined depth at the Z-axis.
Like in face milling, you’ll be able to achieve your objective depending on the accuracy of feed rates and cutting speeds, depth and positioning, as well as clamping force.
Differences Between Face Milling and Peripheral Milling
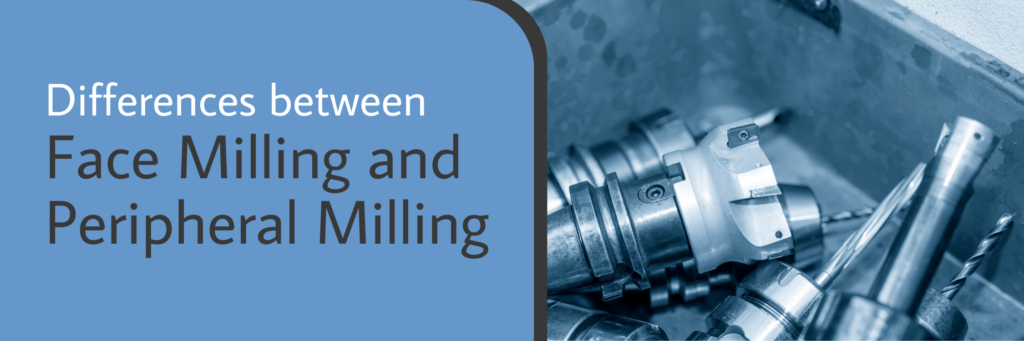
Now that you already know what face milling and peripheral milling are, it’s time to compare the two machining processes. I’ll list all their differences down in 5 points:
- Position – face milling is always positioned at a right angle to the spindle, and the rotating cutting tool is placed perpendicularly to the mill. On the other hand, peripheral milling always follows a parallel direction, and the milling cutter is parallel to the mill.
- Direction – in face milling, the tip of the milling cutter presses against the workpiece, while the cutter’s sides grind the top of the workpiece in peripheral milling.
- Flat vs. Peripheral – the face milling operation is done using the flat face of a milling cutter, where multiple teeth are found on both the periphery and face. On the contrary, you’ll be using the peripheral teeth of the cutter in peripheral machining operations. In this case, the cutter teeth are only on the periphery.
- Purpose – face milling is mainly used for finishing operations, as it aims to create a textured or smooth surface finish on the workpiece. Peripheral milling, on the other hand, is used to machine flat and formed surfaces. Such an operation is dependent on the axial contour of the cutting tools. This process is more effective in removing more material, unlike face milling, which only removes a minimal amount of materials.
- Spindle machines – face milling processes can be done on both horizontal and vertical spindle machines. But peripheral milling is only performed on horizontal spindle machines.
Tips for Milling Operations
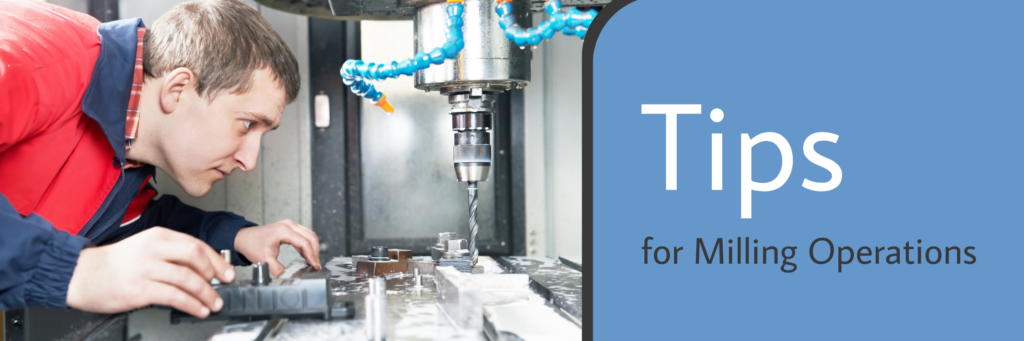
At this point, you already know the difference between face milling vs. peripheral milling, and you’re probably ready to head to your workshop to start milling. But before you do, allow me to give you some useful tips!
- Use a fly cutter with softer materials and shell mills for harder workpieces, specifically steel.
- When face milling, the cutter must be positioned off-center from the workpiece, and the toolpath must be kept on the face milling part.
- AVOID face-milling holes and slots on a workpiece.
- Feed the workpiece against the milling cutter to direct the pressure of the cut downward so the cutter presses and holds the workpiece against the table.
- The part of the workpiece where you’re trying to set the depth should touch the revolving cutter.
Frequently Asked Questions
Let’s answer a few more questions before you go!
What Are the Two Types of Peripheral Milling?
The two types of peripheral milling are conventional milling and climb milling.
In conventional milling, you will see the cutter grind in the opposite feed direction. On the other hand, the cutter grind towards the feed direction in climb milling.
The latter is said to effectively improve tool life.
What is Z-Level Milling?
Z-milling is the type of milling operation that aims to remove material in planar levels perpendicular to the fixed tool axis.
Conclusion
Now you know how to differentiate the two milling operations. And hopefully, you were able to understand how these processes work.
Wait no further and start milling your workpieces. As you head back to your workstation, remember to follow the tips listed above!