Disclaimer: As an Amazon affiliate, I may earn a small percentage from qualifying purchases. This is at no extra cost to you. Learn more here.
Last Updated on December 21, 2023 by Charles Wilson
Milling machines are among the most popular and practical machinery in various sectors.
However, milling machines come in various types with complex functions, designs, and objectives.
I thoroughly described milling machines and their parts, functions, and uses in this article.
To help you decide which machine best meets your demands, I also compiled the various types of milling machines. So let’s start now!
KEY TAKEAWAYS
- Milling is the term for removing bits of the material parallel to the tool axis, and milling machines are the tools used to carry out this operation.
- Most machinists refer to it as a horizontal milling machine, even if other people refer to it as a plain milling machine. This is because, unlike a vertical mill, its spindle is parallel to the worktable rather than perpendicular.
- There are vertical and horizontal machining centers on modern computer numerical control milling machines.
Milling Machines: What Are They?
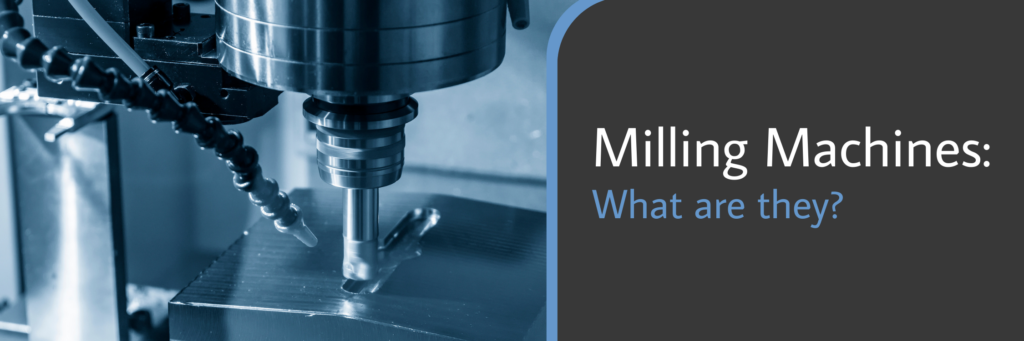
A revolving milling cutter’s cutting motion causes metal to be removed during the milling process, known as milling. These tools can cut, drill, and bore a variety of materials.
The milling machine is one of the most crucial tools in the workshop as a result. All milling operations in this machine can be carried out with high accuracy.
The workpiece is fed against the rotating cutter. Due to the cutter’s numerous cutting edges and rapid rotation, metal is removed relatively quickly.
Because of this, milling machines are frequently used in manufacturing tasks. There are many different types of milling machines, and they are used in multiple sectors.
How Milling Devices Operate
Lathes and milling machines are used to produce similar outputs in many respects.
However, milling machines hold the workpiece motionless using a vice or fixture, unlike lathes which rotate the workpiece.
Milling machines use endmills and other cylindrical tools to remove material. Although they may also deal with contoured surfaces, milling machines are mostly used on flat surfaces.
Parts of the Milling Machine
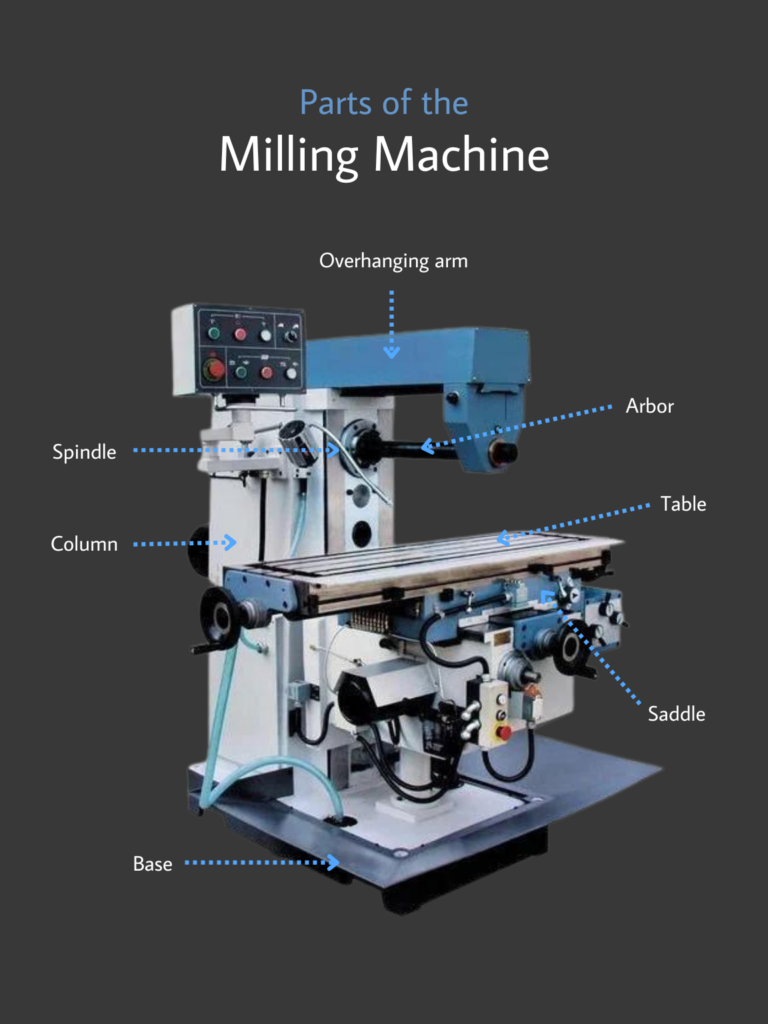
Following are the different parts of the milling machine:
- Base: All other parts that sit on the machine’s base, which is made of a grey iron casting, are supported by it. The hollow base of some other milling machines serves as a cutting fluid reservoir.
- Column: The primary supporting frame mounted to the base is the column. The spindle and feed table driving mechanisms are housed in the box-shaped structure.
- Saddle: The saddle, which slides on guideways precisely 90 degrees from the column face, is mounted on the knee. By engaging a nut on the bottom of the saddle with a crossfeed screw near the top of the knee, crossfeed is applied by moving the saddle horizontally, either manually or mechanically.
- Table: It moves longitudinally while resting on the saddle’s guideways. Accurate T-slots are supplied for clamping the work and other fittings, and the table top has a polished surface. Under the table is a lead screw that fits into a nut on the saddle and enables manual or mechanical movement of the table. Fixing trip dogs to the table’s side may limit the longitudinal mobility of the table. The table of universal milling machines can also be turned horizontally.
- Overhanging arm: The arbor is supported by overhanging arms. It is bearing support for the other end of the arbor and is fixed on the top of the column, extending outward from the column face.
- Front brace: It is additional support that the knee and arbor are given tightly. Between the knee and the overarm is where the front base is fitted.
- Spindle: The machine’s spindle, situated at the top of the column, transfers power from the engine to the arbor via belts, gears, and clutches. An arbor and different cutting tools can be put into the tapered hole on the front end of the spindle, which protrudes from the column face.
- Arbor: A milling cutter is firmly fixed and turned on the arbor, which is part of the machine’s spindle. These are constructed with taper shanks for correct alignment with the machine spindles’ taper holes at their noses. The arbor’s taper shank matches the self-release or Morse taper with a value of 7:24.
Knee and Column Milling Machine
The term “knee and column” refers to the most popular types of milling machine.
The knee and saddle in this milling machine are rotated using a vertical column attached to the bed containing all the gear drives.
The knee of a knee-type milling machine is in charge of giving the workpiece, which is situated at the machine’s base, vertical or up-and-down movement.
In my opinion, column milling machines are the simplest type of milling machine.
You’ll notice a saddle fastened to the upper part of the knee. The saddle can shift transversely. Column milling machines are generally used to create car parts.
1) Vertical Milling Machine
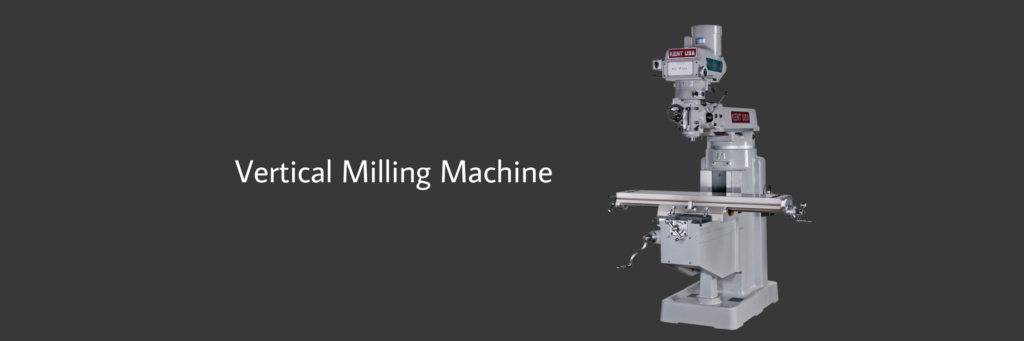
One of the most popular types of milling machine, the vertical milling machine, has a vertical spindle on which milling cutters can be attached for various milling processes.
The milling machine has flat surfaces, slot keyways, twist drill and boreholes, machining grooves, and angular surfaces.
The spindle head of the vertical milling machines is fixed with a vertical column.
The material from workpieces composed of metals, wood, plastics, etc., is removed using various cutting instruments with cutting edges in vertical milling machines.
The work table of vertical milling machines moves perpendicular to the spindle axis horizontally from right to left, in and out, and occasionally up and down.
For me, this equipment is more complicated than a drill press because of the vertical spindle movement and the cutting choices available on a moving table.
A select few vertical milling machines have an upper-cutting head turret that may rotate, improving the machining options.
How to Use It
- Boring or drilling: Vertical milling machines offer a way to create accurate indices and holes.
- Accurate Cuts: Keyways, slots, slotting, flats, and other shapes are accurately cut using vertical milling machines.
- Milling: The workpiece is given a spot or a flat surface during this procedure. For workpieces with uneven shapes, the facing procedure is typically performed.
When to Use It
By removing stock, usually from metallic work parts, the vertical milling machine is a precise rotating cutting tool used for shaping and construction.
Vertical milling machines are used for machining grooves, slots, etc. The mill can also machine plastics and other materials depending on the tools and material.
2) Horizontal Milling Machine
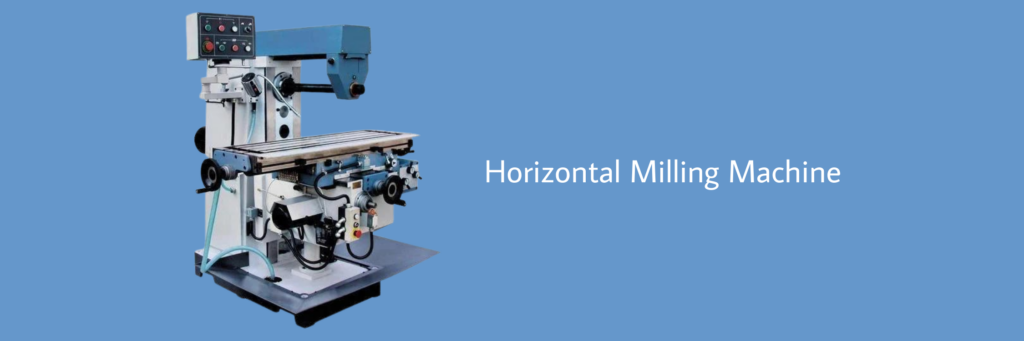
Most machinists refer to it as a horizontal milling machine, even if others refer to it as a simple machine.
Although the horizontal milling machine operates in three axes, the cutting tools will be positioned horizontally, just like vertical mills.
In addition to having a horizontal spindle, horizontal milling machines differ from vertical mills because they can use a horizontal arbor with multiple cutting tools.
Because they are more durable, horizontal milling machines are more likely to be used for roughing cuts and larger workpieces.
Compared to vertical milling machines, horizontal milling machines have special cutting tools. Pressure is applied to the workpiece to remove material from the workpiece.
How to Use It
The spindle, which holds the cutting tool in place, is oriented horizontally in horizontal milling machines, as the name implies.
While spinning about this horizontal axis, the rotary cutter scrapes the surface and removes material from the workpiece.
When to Use It
Projects with requirements like these are acceptable for a horizontal milling machine:
- Groove cutting
- Slot cutting
- Gear cutting
- Side-oriented detail work
- Projects with multiple sides that require cutting
- Projects that require large, heavy, or bulky materials
3) Universal Milling Machine

The universal milling machine, which can be configured as either a horizontal or vertical milling machine, is one of the most versatile types of milling machine you can purchase.
This versatile milling machine becomes more adaptable when additional accessories like a rotary table milling machine, slotting attachment, or indexing head are added.
The universal milling machine can produce a rotating cutter, reamer, twist drill, spiral, bevel, spur, and many other items.
Universal milling machines allow you to carry out every action that a shaper machine can.
A worktable that can swivel up to 45 degrees on both sides to enable helical milling aids in this.
A universal milling machine is capable of performing a variety of milling operations. This machine can also be used for helical milling.
How to Use It
A moveable ram with a drive motor running on dovetail ways is located above the horizontal spindle.
On the other end is a universal spindle head that may be positioned using the attached overarm as a vertical milling head or rotated to either side.
For line-boring or gang milling with multiple cutters, the vertical spindle can be removed and swapped out for a horizontal spindle arbor support that is put on the way.
When to Use It
A universal milling spindle head suspended above the extended table surface of universal milling machines allows them to work with various solid materials.
Due to heavy-duty cast iron construction, these milling machines are often robust.
Fixed Bed Milling Machine
As the name suggests, a fixed bed-type milling machine has a firm bed attached to the machine.
The saddle and knee of bed-type milling machines cannot be adjusted.
It is positioned on the machine’s spindle and has a moveable spindle head. Bed-type milling machines can move both horizontally and vertically while cutting.
The worktable is positioned on a fixed bed in bed-type milling machines, allowing the X and Y axes to move longitudinally.
Therefore the bed cannot move vertically. Instead, the vertical spindle serves as the bed mill’s vertical axis (Z-axis), giving it the ability to offer a 3-axis range of motion.
Bed-type milling machines are chosen for larger projects and heavier workpieces since they are often more robust than knee mills.
For a thorough discussion of the differences between bed and knee milling machines, click here.
1) Simplex Milling Machine
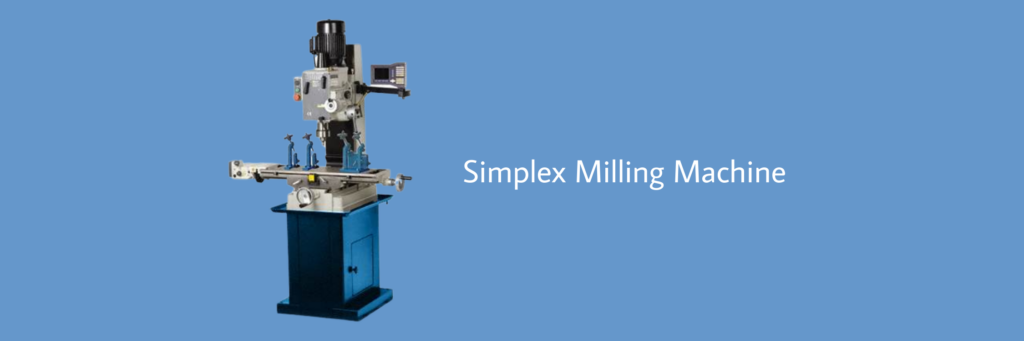
A simplex milling machine can only move in one direction, which is typically vertical.
Simplex milling machines feature good surface smoothness, the flatness of milled surfaces, stability during milling, high productivity, long tool life, and minimal upkeep requirements.
2) Duplex Milling Machine
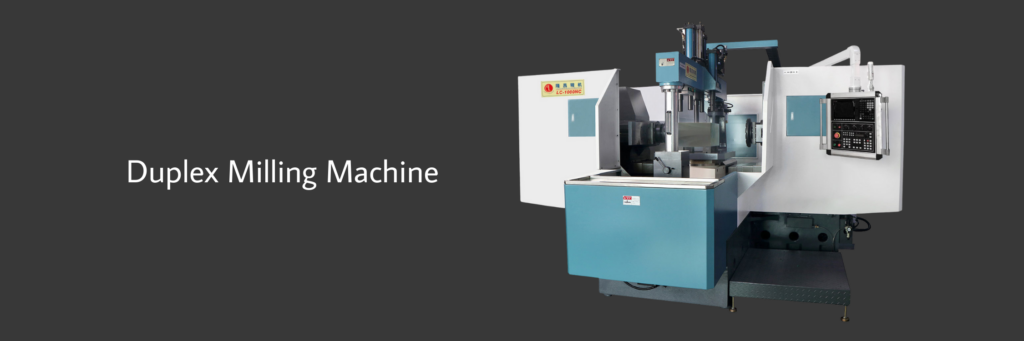
A duplex milling machine is a combination of two machines arranged across from one another. Both vertical and horizontal movement is possible for the spindle.
When the workpiece is machined with two spindles at once, the two machines of duplex milling machines can operate independently or together.
A single person can manage duplex milling machines. Additionally, a duplex milling machine might be either a manual or a CNC machine.
There are various setups for duplex milling machines, including pendulum working regions, a single working area, and a pallet changing system.
Duplex milling machines’ high productivity might lead to a quick return on investment.
3) Triplex Milling Machine
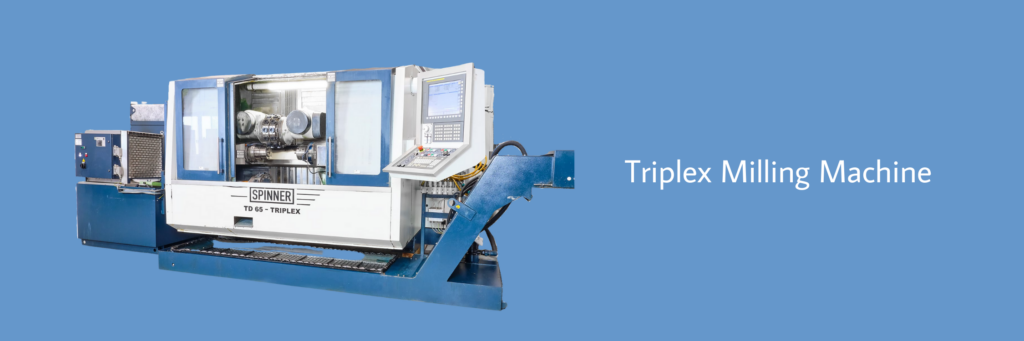
A triplex milling machine is extremely prolific and accurate. The spindle of triplex milling machines may travel in three directions, including the x, y, and z axes.
Applications that are centered on the accuracy of the customer’s requirements are ideally suited for triplex milling machines.
Turret Milling Machines
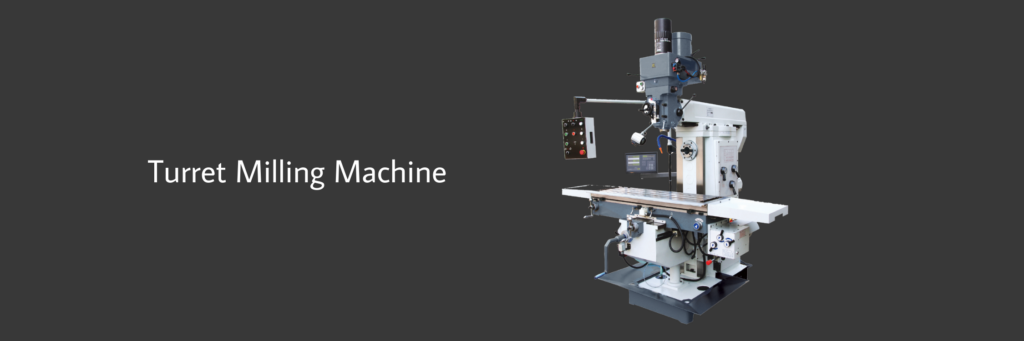
Turret milling machines are extremely adaptable and are typically used to make various parts.
Bridgeport-style milling machines, also known as turret milling machines, have repositioned openings and various functions.
These machines are very versatile machines and are generally used for creating various types of parts.
C-Frame Milling Machine
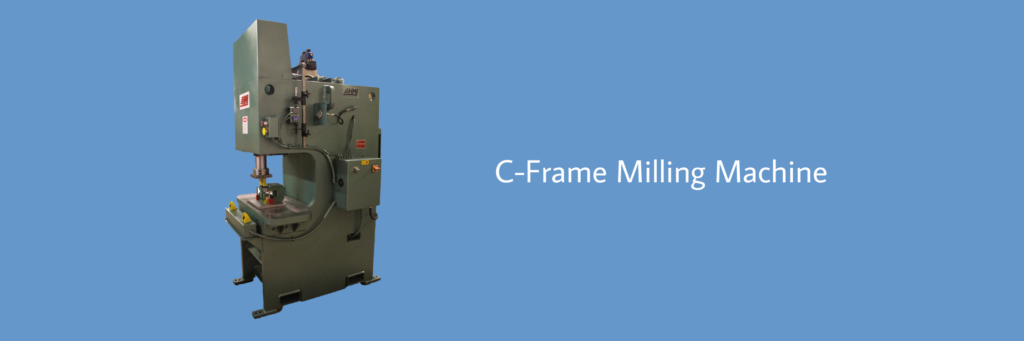
These devices are sturdy and powerful. The hydraulic motor is used to operate the C-frame milling machine. They are perfect for usage in industries.
C-Frame milling machines are made for making identical parts based on a master model.
Grooves and contoured surfaces are typically machined using tracer-controlled milling machines.
Planer Milling Machine
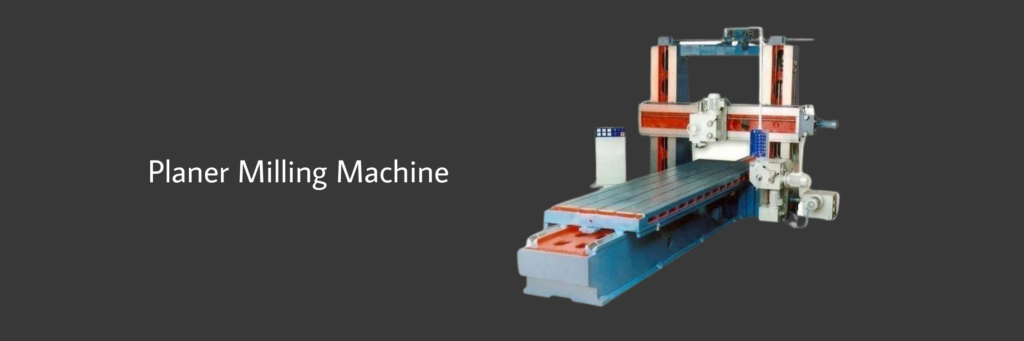
A planer-type milling machine is large and handles heavy-duty operations; these milling machines are also known as “plano millers.”
The spindle head on this machine can be moved both horizontally and vertically.
The planning machine is comparable to and related to the planer-type milling machine. These milling machines have cross rails that may raise and lower the rotary cutters.
Rigid uprights hold up and support their heads, saddles, and both. The movement of the table is the key distinction between a plano miller and a planer.
In a planer, the table moves to enhance cutting speed, whereas, in a plano miller, the table moves to provide feed.
Special Types (Milling Machine)
These unique milling machines carry out tasks that other milling machines cannot.
The special type machines contain a spindle that rotates the cutter and a feature that allows the workpiece or tool to be moved in various directions.
Here are a few of the standard special-type milling machines:
1) Rotary Table Milling Machine
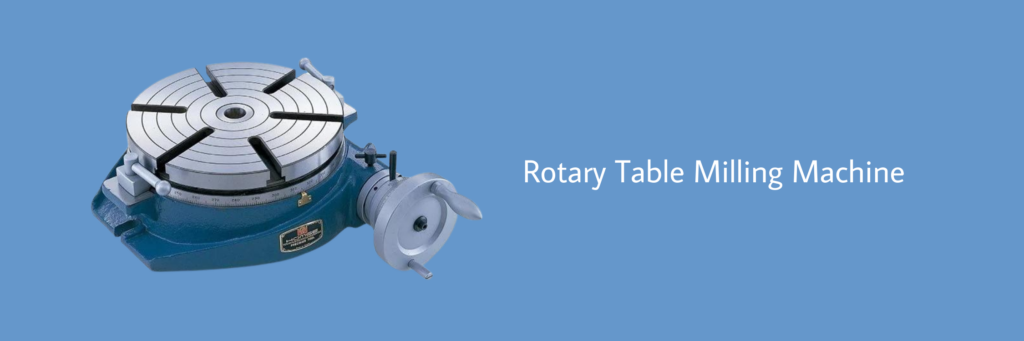
The rotary vertical axis centerline is radially aligned using rotary table milling machines.
On end or around the cylinder, a rotary table milling machine can run up to machine cycles of 2D and 2.5D.
Multiple cutters must be positioned at various heights. It often clamps to a vertical milling machine and allows for cutting round shapes or precise positioning.
The most important benefit of the rotary table milling machine is that the operator may continually load and unload the workpieces while operating.
A rotary table milling machine can be manually controlled or by a CNC milling machine (computer numerical control).
2) Tracer Controlled Milling Machine

With no coding required, a tracer-controlled milling machine is a sort of milling machine that can readily recreate or reproduce the prototype item.
Tracer-controlled milling machines used a stylus to follow a pattern, typically made of wood and constructed by skilled wood patternmakers.
These milling machines are used for machining grooves, angular surfaces, cams, etc.
A tracer-controlled milling machine is ideal for replicating complex and asymmetrical dies and tracing the components.
There aren’t many tracer-controlled milling machines with servomechanisms and those with sophisticated arrangements.
Procedures involving cavity machining process, like die sinking, are carried out on three-dimensional duplicators or profilers.
3) CNC Milling Machine
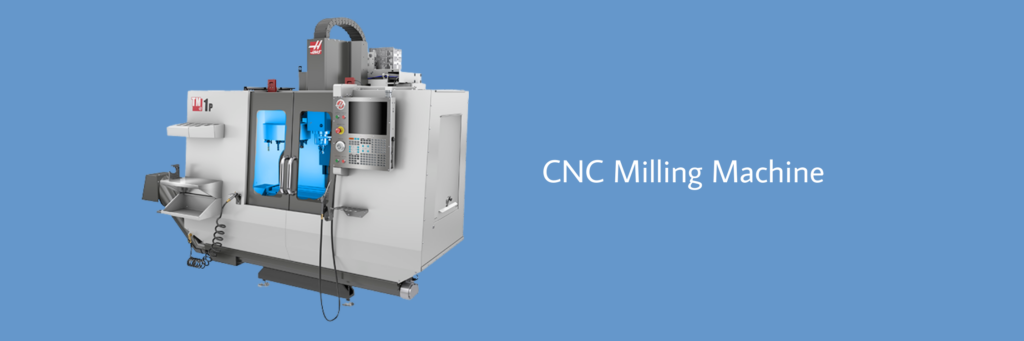
The CNC milling machine (computer numerical control) is the most adaptable, and you must use a computer to manage its functions. It has a rotating cylindrical cutter.
With CNC milling machines, the table can rotate 360 degrees, and the spindle can move in all three directions.
A CNC machine is also perfect for custom-designed parts needing accuracy, detail, and a better surface polish because they can produce complex forms.
Materials, including ceramics, polymers, and composite metals, make up the components of CNC milling machines.
Drum milling machines, C-frame milling machines, and simplex milling machines once occupied a large portion of the space that CNC milling machines now occupy.
4) Drum Milling Machine
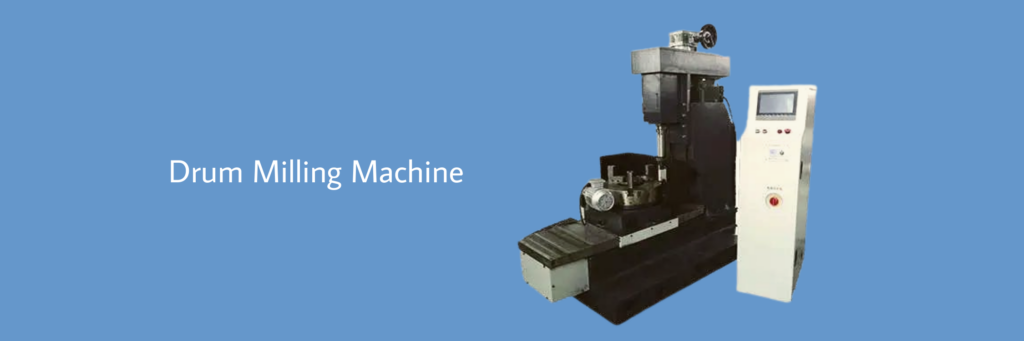
The drum milling machine resembles a rotary table exactly. Like rotary-table millers, drum milling machines offer to finish and roughening cutters.
The sole distinction is that this machine only has horizontal rotation and has a drum-shaped table that holds the workpiece.
When drum milling machines are used, the cutter rotates slowly while pushing the work against the rotating cutters.
You must set the workpiece on the drum to remove the metal. Three or four spindle heads are present on these cutters.
You must take the finished components off and fasten the fresh ones onto it after one full round. Drum milling machines are generally used in industrial operations.
Frequently Asked Questions
Here are some of the most often-asked queries regarding various types of milling machines and other significant subjects.
What Is the Most Common Type of Milling Machine?
Knee and column milling machines are the most prevalent kind.
The knee and saddle are rotated by this machine’s vertical column, comprised of all the gear drives and attached to the bed.
What Milling Machine Is Recommended for Beginners?
With affordable startup costs and significant upgrade options, the Klutch Mini Milling Machine is a fantastic choice for novices.
What Milling Machine Is Best for Home Workshop?
One of the types of milling machine we suggest for most people is the Grizzly Industrial G0781-4, which stands out as a top hobbyist/workshop market brand.
What Is a Thread Milling Cutter?
Thread milling cutters are used to cut thread by milling.
Thread mills are employed on numerically controlled machining centers (NC) with simultaneous triaxle control and helical interpolation features.
Conclusion
There is only one last issue to be answered now that you are aware of your possibilities for the best milling machines: Which kind of milling machine is ideal for you?
You now know the primary categories of milling machines used for cutting and shaping materials in practically every industrial area.
The next step is to choose a firm that will pay attention to your needs, learn them, and provide the best solution in the form of a machine that works well and takes little upkeep.
We hope this tutorial has helped you better understand how milling machines differ. Choose the equipment that best suits your demands. Have fun milling!