Disclaimer: As an Amazon affiliate, I may earn a small percentage from qualifying purchases. This is at no extra cost to you. Learn more here.
The lathe machine is the most common and oldest equipment to be used in industries to turn, cut, groove, drill, and do other machine-related operations into a cylindrical shape. As it is a machine, from time to time, there can be problems. And many common lathe machine problems have solutions.
So if you run into a problem, that does not mean you need to get a new machine. You can overcome those problems.
If we put the problems into a list it will go like this-
- Metal lathe chattering
- Weird vibration on a wood lathe
- Carriage problem
- Threads cutting issues
- Improper metal cuts
- Tailstock slipping
- Lathe machine fails
After years of learning and making mistakes, I have now overcome such unwanted problems, or at least I know what to do.
So today, we will be discussing these problems while working with mini and midi lathes. We will also talk about viable solutions so you can avoid them in the long run.
Let’s dive into the main part now.
1. Metal lathe chattering: Tricks That Work
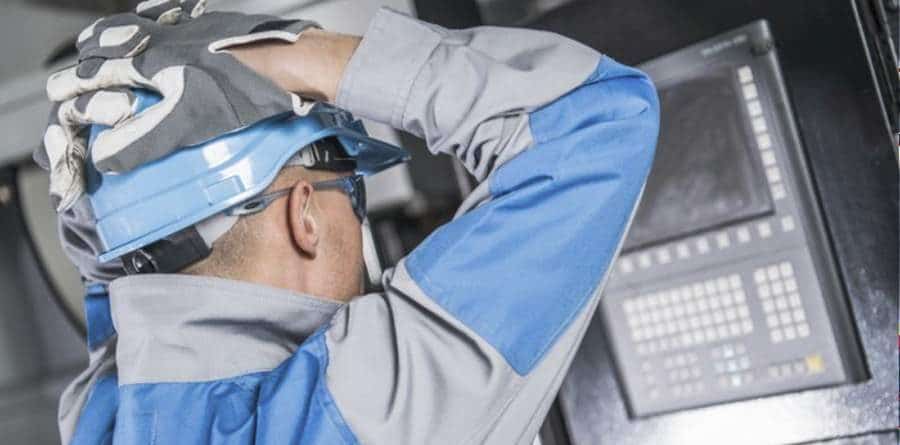
Chattering is the enemy of every machinist that you will face it sooner or later unless you are a CNC machinist and familiar with the HAAS Automation’s SSV technique.
But for the regular machinists who are using general lathes like a small-sized lathe or a lathe mill combo, it can get tricky.
Just to provide a simple explanation to a beginner, I would like to add that chattering occurs when the tool bit catches the metal workpiece during cutting, and it keeps catching in the same place.
Therefor will create a rough cut surface and leave the chatter mark in the metal piece. It’s like a car tire leaving its mark on the dessert. And the sound it makes is the chattering noise.
The golden rule to stop chattering is to “reduce the speed and increase the feed.” Chatter frequently originates if you are going too high in speed or you’re not hitting it strong enough.
If the golden rule here is your first frontline of defense then you can eliminate chatter even with a lightweight lathe also.
Though some operations are destined to chatter, there are few things you can always do to win over.
Step 1: Make sure the rigidity is higher
- Chatter occurs when your cutting pressure is too high than the rigidity of your setup. Rigidly is critical in overcoming chatter. Always make your setup as ridge as possible.
- Check all of your slides are tight enough, nothing is loose. You can also remove your compound if you are not using it. Make sure everything is locked firmly before starting.
- Using tailstock every time possible is a good practice.
- Just keep everything close and tight is the key to maintain rigidity.
Step 2: Decrease Tool Pressure
- Check out your tool bit how it is shaped, how you want your finishes. If you are going for deeper cuts, using a rounded nose tool for a more delicate finish, the tool pressure will be higher.
But we want to lower the pressure. So to manage that, I would suggest you go for lighter passes—a legit and straightforward way to do it.
Step 3: Some other tricks that work
- Flip the tool upside down and the machine on the other side of the hole. It will make the springy toolpost/top slide/carriage act in a completely different way and might be the one trick to get away from chatter.
- Sharpen your tool bit and then try to do a pass that’s deeper than the chatter area. You will be able to remove the chatter marks.
- Wrapping elastic bands or sticking plasticine around the work can be a good trick. You can also use Lead solder wire. It does the same thing.
- I saw a Hardinge demo where they turn a 1″ bar down to 0.5mm in one hit with a knife tool. So if the component has a fragile part, try to finish it to size in one hit.
- Check if the tool is well above the centerline when boring.
- Make sure the top slide is locked in place if you have a tool post on the top slide.
- Put a bolt & nut under the tool against the carriage top and tighten it to provide more support for the tool.
- Using chatter grease or spray does help.
Final suggestions
The more substantial the machine is, the less it will be tended to chatter. So I recommend always go for the heaviest machine you can afford. Look at your manufacturer’s descriptions and lubricate them as per requirement. It is essential to use proper lubricant for the parts.
2. Vibration Problem in Wood Lathe: 10 Tips
Unlike a great quality wood lathe, vibrating issues occur for numerous reasons. It could be a balancing problem. Maybe the wood is not centered well, or the machine itself could have mechanical issues, and so on.
If you look deeper into the source of the vibration, you would typically find two things,
- It’s coming from an imbalance situation of the lathe attached to the ground.
- The problem is between the work-piece and the cutting tool.
So today, I will share ten healthy tips to help you check and solve the wood lathe vibration issues for good.
Try to reach to the core of the problem. The solution will come out quickly.
Priority 1
- Run the lathe without attaching anything. Did you notice any vibration? Then it indeed is a mechanical problem. Call your manufacturer or take help from a local turning club.
- The more solid and robust the attachment of the wood chunk is with the faceplate, the more it will reduce the vibration.
- Irregular large bowl blanks produce the vibration pretty often. Run the lathe and increase the speed gradually in this case. See at what point the chunk is turning smoothly. Start your project from there.
- Checking your leg extension if it’s settled with the floor in a proper flat situation is critical. If you see any imbalanced surface contact, you can either move the whole lathe to a new place or just use a flat rubber piece or a chunk of paper folded. Put it right beneath the leg where the surface is not contacting smoothly.
- You can put some extra weight on your lathe if it’s possible to ground it more firmly. It will absorb the movement more to the ground. It’s not recommended but still effective. It helps. Try damping the vibration with sandbags on the lathe legs /shelf.
Priority 2
- If you are working with thin woods and experiencing vibrations, this is where steady rests are a must-try option, no matter if you are turning spindle or bowl. There are steady rests specially designed for bowl turners now.
- Check if your motor, drive belt, or headstock bearings are making any noises. You may need to change them if possible or at least repair it.
- Try to use the tailstock almost every time. Tailstock is all about the support. You need your workpiece to be mounted firmly between the centers. So it is evident that it dramatically reduces the vibration.
- If the motor does not have the vibration, then trying to mount the motor rigidly won’t help that much. Check out the leg again and try to isolate the motor entirely from the stand. It’s a personal suggestion, so please take the help of an expert describing your situation.
- I always take some time to clean the headstock. It sounds simple, but it can be critical sometimes. Whether it’s metal dust or wood, if it gets inside the headstock, it can move the faceplate or chuck a little bit from the center. So be cautious.
Important things to remember
Contacting directly to the designer of your lathe is the best practice when it comes to repairing or even replacing any bearings, belts, or motors. They can give you the best advice that suits your lathe.
Always use sharper tools or sharp them regularly. Whether your vibration is coming out from the tools or the work-piece, it is the best practice.
And remember turning at a higher speed won’t make you any specialist at turning. It’s not about the speed. It’s about perfection.
3. Carriage Problem
With time you can get a ‘stuck carriage’ in your lathe machine. Not only the carriage but the handles also need to be working perfectly for the machine to move and run efficiently.
Just to remind you that you need to have a clear knowledge about the carriage system on a lathe machine to point out the exact problem whether it’s a mini metal lathe or a heavyweight lathe.
Carriage helps the cutting tools to move in between headstock and tailstock.
- At the top of the carriage, it is the Toolpost that holds the cutting tools.
- Compound rest holds the tool post and has a handle to rotate it to any angle for making different cutting angles with the tools.
- Cross slide holds the tool rest, and the compound rest together. Has a handle that helps to perform the up-side movements of the tool post and compound rest together.
- Then comes the saddle that holds all the components mentioned above. It moves right to the left also by a handle.
All together they are called Carriage in short.
Suggestions
See which part of your machine is not working properly. (Not sure what the part is called? Check out our post about parts of a lathe.) If your cutting tools are not sitting in a fixed position then the problem is in your tool post.
Similarly, if the cutting tool is fixed but you are still feeling wobbly then check out the compound rest underneath the tool post.
Strip the carriage down to make sure all the assemblies are in good shape. Tight up the nuts properly if you find them loose. Wash off the grease.
Double-check if the surface of the compound rest is flat.
These should be enough.
4. Threads Cutting Problem: 2 Steps
I don’t exactly remember where I heard that but there is a saying, “To cut threads on the lathe, you must become the lathe.”
That means you have to stick to it for some time if you are really into threading operation, and I promise you will get there.
As a beginner, the most challenging part you will face is when you start cutting them. The same question will keep hunting you when the knob gets turned and why does it happen, etc.
Let’s give you some tips to make it easier for you before you start.
Step 1: setting up the lathe for threading
- Your compound and toolpost must be clean and steady. Check that first before running your project. It should be fine if that’s a new lathe.
- Always use the manual from the manufacturer of your machine to select the right gear you need to cut the thread. Look for the gear table in the book.
- Then set the threading tool to the diameter of the part to be threaded. It will be your starting depth.
- The scale should be set to zero both for the cross slide and the compound.
Step 2: Start cutting the thread
- Start with aluminum instead if it’s your first project. It will make life a bit easier.
- Run the lathe at a slower speed, and start cutting a scratch pass. Needless to say that you need to set a zero position before that.
- Stop the machine whenever you run the tool at the end of the cut. Do the cut one at a time to avoid any damage.
- Use a thread gauge to double-check the pitch after one scratch pass.
- Back the carriage away to clear the tool. Run the lathe again, but in reverse, to track the tool back to the start point.
- The tool will not touch the material while backing off the carriage. Then go for the next pass.
- Turn the carriage to scale zero again. The compound and the cross slide.
Important Notes
You need to increase the depth slightly that you set to zero for the compound every time you complete a run.
Repeat the full process a few times. Slowly but surely you will master it. Make some time to clean up the tools every hour.
Stay focused.
5. Improper Metal Cuts
If your lathe cutting tool has not been installed properly or you are ignoring the proper tool height settings, you are likely to have improper metal cuts.
It will ruin your projects and you will never be satisfied. The trick for perfect installation is to remember to get accurate and immaculate cuts.
Now let’s see how can we take the right actions so we can get out of it.
- Before you start working, do not forget to center the lathe tool correctly. Remember it’s critical. You will have a hard time if your lathe tool is not centered perfectly.
- Getting the right cutting tools for your lathe is a fundamental thing to start cutting. Now that depends on what machining operation you are up to. Say for example- in terms of turning or facing, carbide or high-speed steel tools normally are the go-to options.
- Select the cutting tools you can sharpen easily. Take Carbide woodtunring tools for example. They are easy to repair and sharpen if gets worn.
- Do not forget to set the “tool height” correctly. Because if the center rotation of the chuck is interrupted, then say bye-bye to smooth cutting.
- One more very vital thing to keep in mind is that if the workpiece is not supported by the tailstock, the piece will loosen up very easily during operation. That can be catastrophic.
- Pause the machine frequently. Let it cool down and then start again.
6. Tailstock Is Slipping From The Centers
It’s pretty common in woodturning lathe. Abruptly, you may find that your tailstock is slipping while trying to tighten the work-piece between the centers.
This can happen even with the new lathe when the tailstock is not fixed properly before working. Lock it down firmly before you start cutting or turning.
But the problem can be annoying if it’s not a new lathe.
Fix it
For a new lathe, check out the screws properly to tighten the tailstock before starting. If you find them loose, do tighten them well. But what if you are using a lathe that’s been running for some time now and doesn’t have any warranties left?
Don’t be a Macgyver; look for a turning Club in your area if it gets complicated. Be on the safe side. If you think you can do it your own, then this video might help you.
7. Fails
Lathe machines can lead to accidents as well. Safety is a crucial key while working with any machine. Nothing can be better than using safety goggles to protect your eyes from the dust.
Your clothes can get caught within the machine so you must wear proper workshop clothes.
Fix it
Clean the carriage on a regular basis to avoid metal dust on it. Use a brush to take off metal particles but be in the distance as much possible.
This distance can help you avoid the direct contact of metal particles with your skin. These particles may cause scrapes and bruises.
Final Words
That is all regarding some of the common lathe machine problems and solutions. I hope you will find the answer helpful to your question.
If you think this article helped you in some way, share it with your turning buddies. Feel free to comment if the problem persists.