Disclaimer: As an Amazon affiliate, I may earn a small percentage from qualifying purchases. This is at no extra cost to you. Learn more here.
Last Updated on February 28, 2023 by Charles Wilson
When working on a project, it is important to have the right machine tool for the task. Face and end milling operations are often interchanged in cutting or machining processes.
These cutting tools are used worldwide, so it is important to know the difference between end milling and face milling.
If you want to know what makes them different from each other, this article will focus on the difference between end milling vs. face milling.
Key Takeaways
- Face milling is positioned perpendicular for horizontal cutting
- End milling uses both sides and ends of the cutter
- Face and end millings are two of the most used milling processes
- Face milling is the procedure used for creating a smooth and flat surface on materials like plastic, metal, and wood.
- End milling is used to create holes and shapes in materials like plastic, metal, and wood.
What Is Face Milling?
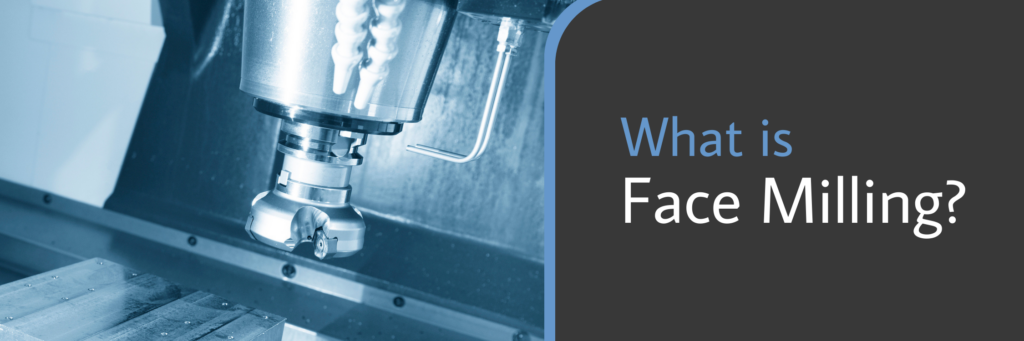
The difference between end and face milling is that a face mill can’t cut axially. One of the reasons is that its cutting edges or cutting teeth are located in its cutting head or at the end face.
In addition, the coarse and fine teeth are also replaceable, which plays an important role in using the milling cutter for a long time as long as you always have good cutting quality.
Another significant difference between a face milling cutter and end mills is that face mills are the best option to achieve a superior surface finish and remove material on the surface.
It is because face mills have more corner radius than end mills, making cutting attainable in a single pass.
Also, they are often bigger in diameter than the workpiece they are going to cut, which makes them a good choice if you want to process the surface in a single pass.
PROS
- Amazing option for different surfaces
- Establishes a flat surface
- Placed perpendicular to the spindle of the machine that can establish holes within the workpiece
- Great for tool life with a bigger diameter
- Reduced chatter and vibration
CONS
- Not the right tool for radial cuts
- It uses a lot of electricity
- No vertical sides
- Can’t be fed in an axial direction
What Is End Milling?
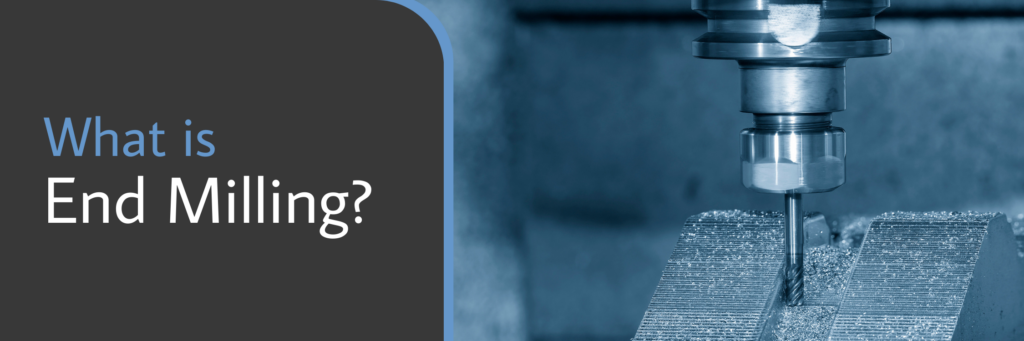
End mills are cutting tools used commonly in wood, metal, and plastic. The cutting edge used by these milling cutters is often shaped like a screw.
Unlike a drill press, whose edges are designed to cut vertically, the end mill has cutter teeth around the edge and face of the cutting tool.
In addition, end mills have different cutting styles. They cut different types of material in a circular motion from side to side.
End mills are popular if you are dealing with a workpiece that needs grinding, slotting, contouring, reaming systems to make openings and forms, and profiling as well.
An end mill comes in a range of shapes, sizes, and styles for different applications and types of processes.
PROS
- Great for pockets and depth
- Cutts material in a circular motion
- It comes in a range of sizes and applications
- Smoother cuts are achieved
- An end mill is often made with high-speed steel or HSS
- Smaller in diameter
CONS
- Milling machines are typically pricier
What’s the Difference Between Face Milling vs. End Mill?

Their significant difference can be seen with the naked eye. Both machines are great for different kinds of milling processes, but both of them serve different purposes.
End mills use both the end and sides of the cutter, while a face mill is bigger in diameter for a complete horizontal cutting. The end mill is designed for depth and pockets and should be as deep as possible.
On the other hand, face mills are intended to create flat surfaces, and when they are plugged in, they have no vertical sides. They are essentially the right cutters for removing a small amount of stock.
Other Types of Milling Cutters
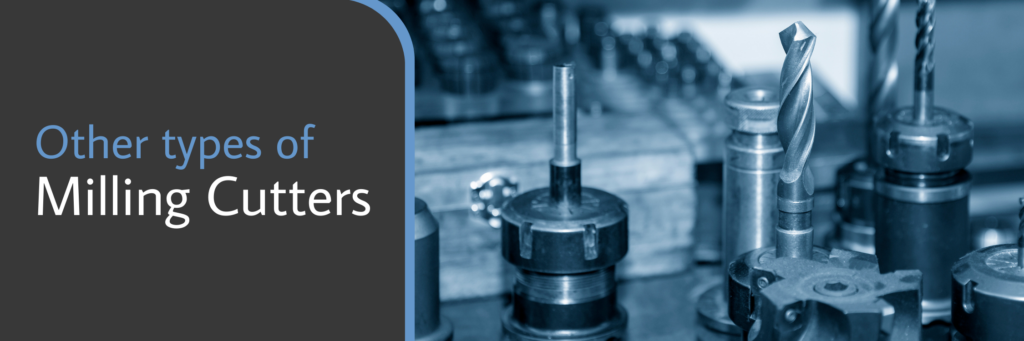
End and face mills aren’t the only tools used during milling.
There are also different tools used in these operations, which is why it is important to know what these tools are to get a good idea of how they operate.
Shell Mill
For face milling, shell mills are definitely the best choice regarding the tools used. Having multiple teeth combined with inserts around the edges makes this type of mill great for finishing the surface.
One of its main advantages is that it can remove any surface material at a time. However, it needs changing when dealing with either soft or hard materials.
Fly Cutters
Unlike face and end mills, a fly cutter only has one cutting edge with a singular insert. But they are the best choice if you want finer finishes without consuming more power.
With lower power consumption, it uses lower speeds to cut softer materials like aluminum or mild steel. These are great if you want less power but finer finishes.
Frequently Asked Questions (FAQs)
If you have further questions about the difference between end milling and face milling, you might find them below.
How Does Face Milling Work?
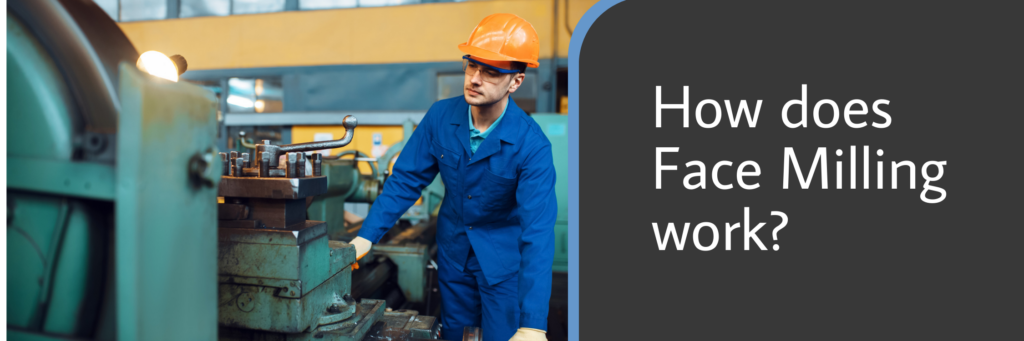
Most machinists using a face mill for different milling procedures divide their process into four segments.
Step 1: Positioning The Workpiece
Most machinists will check whether the workpiece is attached to the machine table to start the milling process. This process is to ensure that the workpiece is stable and avoids slipping.
Step 2: Proper Positioning
When the milling machine is in the right place, the operator will position the face mill perpendicularly to the workpiece. The top part of the cutter will work on the material.
Step 3: Regulating Spindle Speed and Feed Rate
The spindle speed and feed rate are adjusted during the milling procedure. Adjusting the spindle speed is important to ensure that cutting is precise to create a favorable result.
Step 4: Machining Proper
Once everything is set up, the machining proper will begin once the computer sends the code for the process to begin. You just have to wait before the end product is finished.
Can You Bore With a Face Mill?
Yes! Boring and drilling with a face mill is achievable. It’s why a face mill is a versatile tool for different kinds of applications.
Can an End Mill Be Used for Face Mill?
An end mill is a large tool with more flutes capable of cutting in different directions. Although an end mill can be used for face milling, don’t expect that results are the same as using face mills.
How Do I Get a Better Finish With a Face Mill?
Most jobs that aim to achieve a better finish use a wiper flat insert to improve the finish.
In addition, when all things are considered, three factors can lead to a better finish; more lead angle, positive rake, and sharper inserts.
How Deep Can You Cut With a Face Mill?
Face milling in high feed rates is possible using a cutter tool with a small angle when entering the work or using round inserts.
However, the depth range doesn’t exceed more than 2.8mm. Cutters vary a lot depending on the type of work they are cutting. A small entering angle is your best bet to achieve small axial depths.
What Materials Are Used for Cutting Tools?
- Ceramics
- Carbon tool steel
- Cemented carbides
- Diamond
- Cubic boron nitride tool
Conclusion
Most people are typically confused with the uses of both machines. However, they are intended for different purposes and shouldn’t be considered the same.
Still, these machines are great tools for different kinds of work. It’s why you should know their difference, so you have the right tool for the intended purpose.
This article should help you see the difference between end milling vs. face milling debate.