Disclaimer: As an Amazon affiliate, I may earn a small percentage from qualifying purchases. This is at no extra cost to you. Learn more here.
You know something’s not right when you constantly hear a sound from ANY machine. The same goes for your CNC machine, no matter what it’s working on.
If you don’t want to waste your steel bars, you’ll have to address your chatter in machining as soon as you hear it.
Don’t know if it’s your tool holder or how your cutting tool might not be holding well while it’s drilling those pocket corners.
Luckily, I’ll tell you how you can lessen the chattering of your CNC lathe. I’ll also tell you all about how to know the different problems you can look out for.
Key Takeaways:
- Chatter is caused by unwanted vibration during your machining process. It has a sound that we can compare to microphone feedback.
- Reducing chatter is important to prevent wasting your materials and damaging the machine’s service life.
- Changing the spindle speeds tends to be everyone’s first instinct when they hear their machine chatter. It will help your machine avoid reaching a high frequency and reduce chatter.
- If it doesn’t deflect, it won’t vibrate. There are many ways to reduce the deflection of your cutting tool to decrease vibrations.
- Knowing the difference between a tool chatter and a workpiece chatter helps determine what adjustments you need to make.
What Is Machining Chatter?
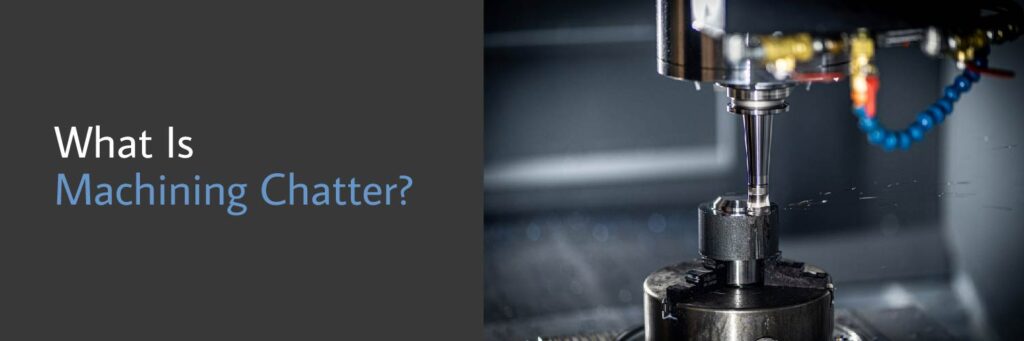
Chatter is a resonant phenomenon that can occur during high-speed machining. The vibrations cause a high frequency that we can compare to a microphone’s feedback.
Besides the sound, you can visibly see the result of the end product of your metal. It results in a rough and uneven cut on your workpiece caused by the vibrations.
It affects the overall outcome of your machining processes and tools, especially when it’s not addressed properly.
If your machine starts to chatter, its vibration will cause an uneven cut on your steel. It will lead to the steel also responding to that vibration, which will make the chatter worse.
If you start hearing your machine chatter, it’s best to stop your machine so you can check what you need to adjust. There might be a loose or damaged part that needs fixing.
There are different kinds of machining chatter which I will discuss later on.
How to Differentiate Chatter Sounds
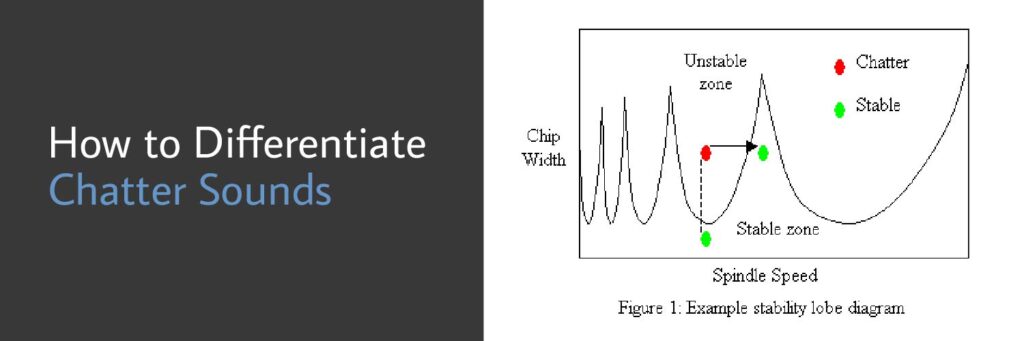
Chatter vibration is generally known to be the high-pitched sound you can hear during the cutting process. However, it can come in different frequencies.
You can identify the three kinds based on their pitch and the end product on the metal. It can be classified into three frequencies:
- Frog Horn: A low-frequency sound that results in large and gentle ripples.
- Horn: A medium-frequency that results in your metal’s surface appearing like fish scales.
- Whistle Scream: A high-frequency that makes the machined surface look like wrinkled silk.
Whatever the chatter frequency you hear, they will all cause damage to your machine, tools, and product.
Why Does a CNC Machine Chatter?
There are many reasons why your machine can chatter. The most common cause is misalignment, imbalance, looseness, or wear.
When an unbalanced weight sits around the machine’s axis, it generates a centralized force. It will then cause the vibration, which we hear as chatter.
However, it can be more specific to the different parts and strategies used during the cutting process.
Once you hear that sound, you can look into these specific factors:
- Tooling: The length and width of your cutting tool may not be compatible with the cutting force.
- Work Holding: More pressure might be needed on the workpiece.
- Machining Strategy: You can’t use the same techniques and cutting forces for every tool path.
- Machine Set-up: Your machine should be on a concrete floor without cracks and other discontinuities.
It’s easy to troubleshoot these factors when you hear chattering.
Read on to find out how you can address these issues.
How to Reduce Chatter in CNC Machining
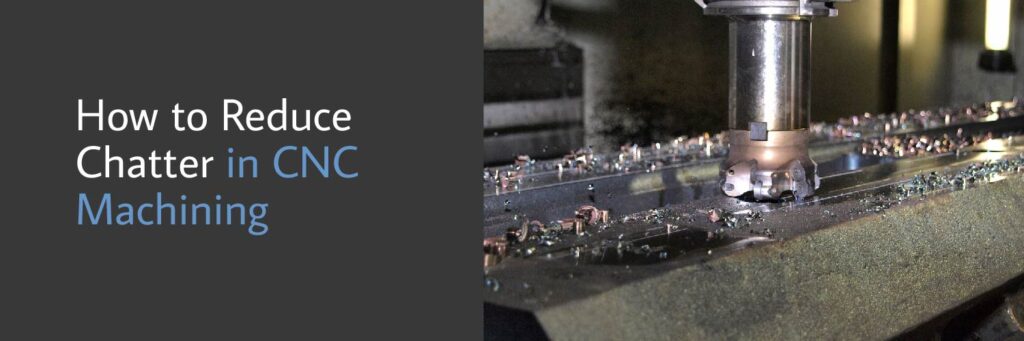
It’s important to avoid chatter vibration to optimize your productivity and prevent damaging your tools.
Sometimes, fixing it could be as simple as checking if your machine is on a solid concrete floor. Other times, you might have to address the chatter in machining within the machine itself.
A chatty tool results in a poor surface finish, which can be dangerous to work with. So if you start hearing a sound, it’s best to check it out and address the issue.
Here are the machining strategies to address your chatter problem.
1. Change Your Spindle Speed
When we hear chatter, the most common response is to adjust the spindle speed.
Giving your spindle speed variation to decrease chatter. It can help lessen the resonant vibration between your workpiece and cutter.
A great example would be when plunge milling is used for a deep cavity. If you start to hear chatter, you may need to slow down.
Your first instinct might be to instantly stop or reduce the speed. Take note of your feed rate when adjusting the speed. Too much material can cause an increase in the chip load.
If the ratio of chip load to your speed is not ideal, it can cause tool breakage.
Changing speeds also doesn’t mean simply slowing down. Sometimes you may need to speed it up, depending on what you’re working with.
The important thing is to get out of the resonant frequency that causes your tool chatter.
2. Realign Your Cutting Edge
Any alignment error with your cutting edge will cause chatter. You would need your spindle centerline properly aligned for accuracy.
Other realignment issues may also contribute to tool chatter.
Double-check if your stick tools are the correct size for your tool holder or turret.
Any alignment issues with your machine tool, in general, causes excessive cutting forces. It’s what leads to the cutting vibration.
If you’re constantly having problems with the realignment, you may need to replace your cutting tool.
3. Reduce Your Machine Tool Deflection
Another way to decrease chatter and vibration is by reducing the deflection of your cutting tool.
If it doesn’t deflect, then it won’t vibrate. No vibrations mean no annoying sounds while you’re working.
Here are the ways you can deflect your cutting tool and minimize chatter.
Minimize Tool Stickout
It’s important to check if any of your machine’s tools are sticking out during your cutting process. Anything that blocks your cutting tool path will cause unwanted vibration.
The less distance between your tool holder and the tip, the better your machine will work.
Remember that a stiff and rigid tool is usually longer. You can use a long stick tool for more clearance. It will serve as support for your tool to provide a steady rest.
Boring bars might also stick out. I advise tightening the screws that hold your boring bar to fix this. You can also get a special vibration-dampening boring bar for extreme distances.
Increase The Tool’s Diameter
Your tool path might not be compatible with your cutting tool. The inaccuracy in small variables, like diameter, has a huge impact on the whole machining process.
Try increasing the diameter of the cutting tool. It will help in reducing your cutting tool’s deflection.
A small change in diameter can make a huge difference with the vibrations it makes and can minimize chatter vibration.
Limit Cut Depth or Width (or Both)
If the first two don’t work out, it’s time for the big guns.
Try to recalculate and change the variables for depth or width. You can easily do this using your program.
Your adjustment would depend on your project. Sometimes, it would be enough to adjust one of these factors. Other times, you might have to adjust both.
Reduce Feeds and Speeds
This factor can also be affected by the former. Once you’ve limited the cut width or depth, you would normally have to adjust the feeds and speeds too.
Unlike a manual machine tool, CNC machining allows us to program changes in how the machining process works.
You can calculate your cutting speed with the equation RPM = (4 x SFPM)/cutter wheel diameter.
You can calculate the feed with the equation FR = RPM x TL x CL, whereas:
- FR = feed rate in inches per minute or mm per minute
- RPM = the speed of your cutter
- T = the number of teeth on your cutter
- CL = chip load or feed per tooth, which refers to the thickness of the material removed by one tooth
The other things you can adjust are the surface speed, separation marks, and the flute cutter.
Try adjusting these variables accordingly to help reduce the deflection of your cutting tool. Adjusting how your cutting parameters will also affect your productivity.
4: Check Your Parts
If there are no changes in your machining vibration, you might have to check the other parts of your machine. Some of them may be damaged or not in the right position.
Try checking on your spindle, machine level, tailstock, and turret. Make the necessary adjustments before trying again.
If the problem persists, remove your way covers and check your linear guide, ball nut, and ball screw. If they’re damaged, you will have to replace them.
Other parts you may need to check on are the cutter tooling, sharp blades, and tool holders. You’d always need the right tool in place to avoid chatter.
There’s also a way to know if you’re using the right tool holders from your tool selection. These would include your vise, vacuum table, and chuck.
To check if they’re the right size, apply clamping pressure as evenly as possible. You’d need sufficient pressure to fix this.
Lastly, variable pitch end mills and chip flutes can reduce chatter. Having them in place will directly affect the resonance from chip loads.
Types of Chatter in Machining
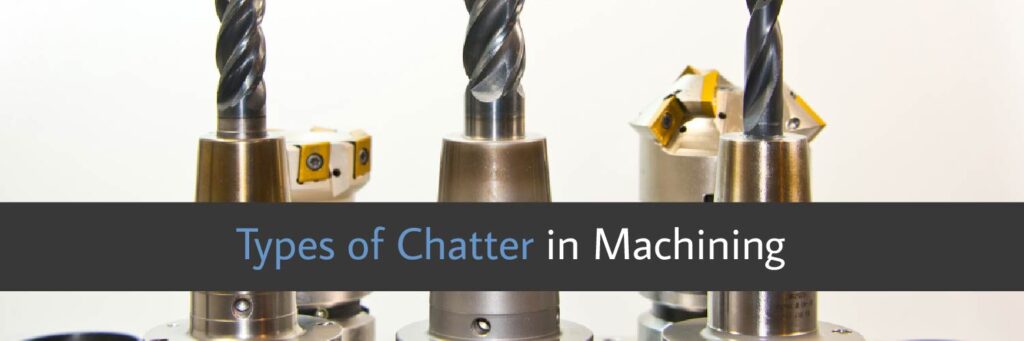
There are two main types of machining chatter, based on which part initially caused the vibration.
It’s important to know the difference between these two. That will help you understand how you can fix the machining vibration.
Tool Chatter
Tool chatter involves your machine and tools.
It’s the common chatter sound you’d hear when you work. Excessive tool chatter is usually transmitted to your workpiece.
As formerly stated, you can easily fix this by tinkering a bit with your CNC machine. Sometimes, you must modify your machining processes to address this.
Workpiece Chatter
Workpiece chatter refers to the vibration from the thin-walled parts of your workpiece.
There is vibration from your workpiece wall caused by its structure, the programming of its cutting, or how it interacts with your cutting tool.
When you hear this, it usually creates more problems for your workpiece material. Its vibrations would also be transferred to your cutting tool and machine.
You can address this chatter the way you would with a tool chatter. Using a filling material would also help improve its rigidity, minimizing chatter.
Why Do We Need to Reduce Chatter?
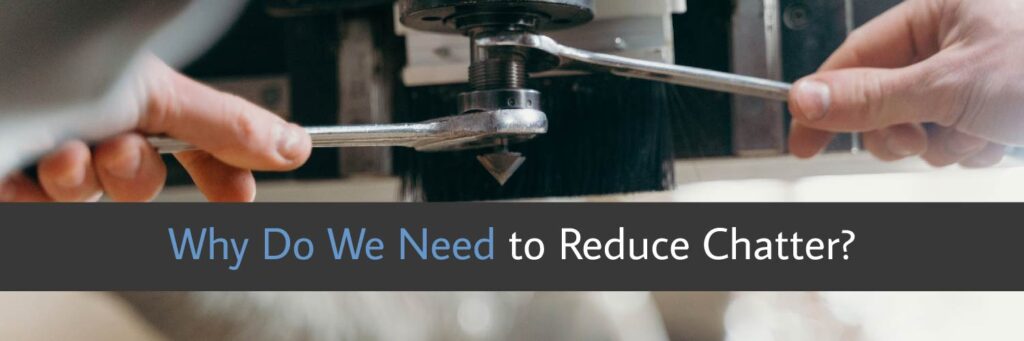
Letting chatter vibration continue while you work isn’t only irritating. It’s a part of the machining cycle that will worsen as you proceed with your project.
Not only will the product be unpleasant, but it will also lessen your tool life.
It’s normal to have some vibrations at a natural frequency. However, a constant high resonance would cause damage and add to your work.
These are the negative effects of chatter.
Reduced Tool and Machine Life
Cutting tools can’t handle vibrating impacts. Constant tremors will also lead to uneven tool wear and damage.
It will also damage the surface quality of your metal. Your productivity isn’t the only thing that will cost you. Tool replacement is very expensive, especially if you need it often from the chatter.
However, it doesn’t only affect your tools. Every little tool in a CNC lathe machine is attached to something bigger.
When one part vibrates, the other parts will also be affected. It would match the same frequency as the initial part.
The vibrations would wear your machine out faster and put the different components under stress. It would also reduce your efficiency and cause downtime.
These should all be addressed to improve your tool life and machine life.
Poor Surface Finish
The vibration of your tool from the chatter will increase the vibration of your surface and vice versa. It will lead to obvious vibration scratches.
The aesthetic properties of your workpiece will be greatly damaged. It would not be easy to repair. Most times, no one can repair it at all.
The poor surface roughness would also affect the quality and durability of your metal. Its visible waviness will diminish its tolerance, especially in extreme situations.
The poor finish of your workpiece may go to waste, given its quality and lack of durability. It will be an added cost to purchase more material for your work.
Reduced Dimensional Accuracy
When you have chatter, your cutting tool is derailed from the path you’ve initially programmed.
This deviation is the result of the bad fitting of your parts. Its inaccurate dimensions may be too tight or too loose, too long or too short. Small changes in your variables and positioning can address this.
The simple derailing of your cutting tool greatly affects the product, your tool, and your machine.
It must be addressed to prevent any further damage to your equipment.
Frequently Asked Questions (FAQ)
You may have more questions about dealing with your CNC lathe’s chatter.
I’ve gathered the commonly asked questions about it to help you work with the chatter of your CNC machine.
Can I Predict Chatter?
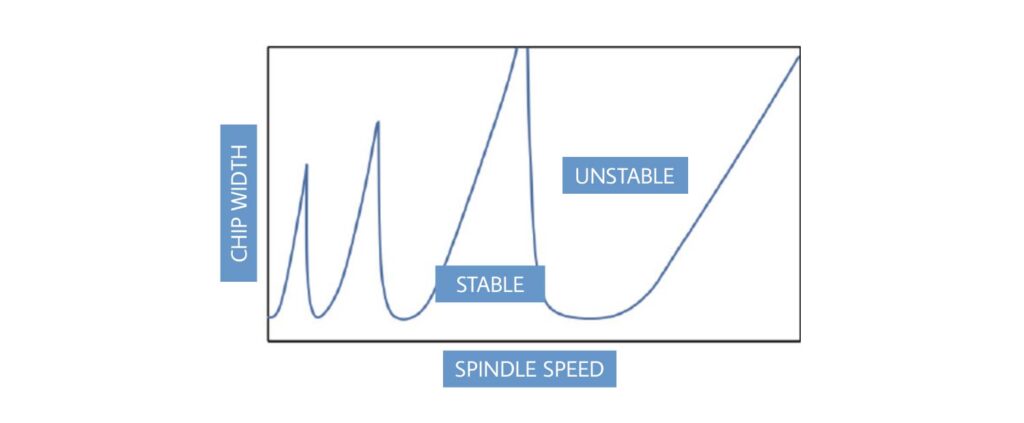
You can predict chatter based on your spindle speed and chip width.
There have been numerous studies on CNC machines in general. They’ve come up with the following graph to help us understand this:
The spikes show the estimates of where you can cut without chatter. The valleys, on the other hand, show where your tool will chatter.
The goal is to find the sweet spot so you can hit those spikes. Doing this won’t only eliminate chatter. It will also help you be more productive while working.
Can I Repair Chatter Marks on the Metal?
Throwing out your damaged workpiece might feel like a waste, especially if the marks aren’t very visible.
If you notice that the tool marks aren’t too bad, you can try matte etching. It should help to even out the damage from your cutting process.
How Is a CNC Milling Machine Different From a CNC Lathe?
Both lathe and milling machines are used to work with metalwork. They’re designed to shape metal to be used for tools and construction. While they may have different uses, both can experience chatter in machining.
A CNC lathe machine is used for machining when both the material you’re machining and your tools are stationary. They’re both held on a turret against each other.
In structure, these tend to be longer and lower in profile. You can compare a CNC lathe machine to a workbench. These machines are usually used for machining round parts only.
A CNC milling machine, on the other hand, holds the material stationary. Then, the tools will do the moving while they cut.
They’re usually used for any shaped part, unlike the lathe.
Conclusion
Whether it’s CNC turning or any other project, you’d want to prevent chatter in machining at all costs.
It can easily cause damage to your machine’s tool life and final product.
If ever you hear a strange sound again or encounter other problems, you can just go back to the tips in this article to help you solve that problem.