Disclaimer: As an Amazon affiliate, I may earn a small percentage from qualifying purchases. This is at no extra cost to you. Learn more here.
Many industries turn to milling machines to fulfill their needs, and mills remain a vital tool in the manufacturing process and a normal sight on the shop floor. However, innovations in machining have helped make manufacturing more efficient: the CNC mill. So how are CNC machines different from manual machines? I’ll be pitting manual milling vs CNC milling here. Let’s begin.
What Is Manual Milling?
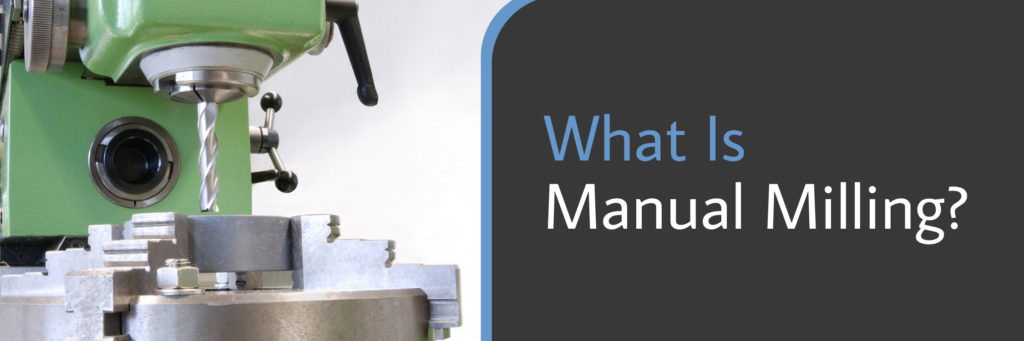
A manual milling machine is a traditional machine shop tool. They can be large enough to stand on their own or small enough to be secured to a work table.
Manual milling machines are designed to remove material from a workpiece and are controlled by a single operator per machine. Manual mills are typically used to remove material from metal workpieces.
Unlike a lathe, manual machining involves rotating the cutting tool around a static workpiece. Manual machining uses various tools to produce parts.
One example is the chamfer mill, used to chamfer features into the workpiece’s surface.
Despite being slower than CNC mills, various manufacturing processes still require using a manual mill, especially anything involving quick repairs on a single part.
If you’re creating a smaller batch of prototype parts and are a precision machinist, manual machining can still be faster than CNC.
Advantages
Some factors keep manual machines in use, even alongside CNC machines.
Quicker to Set Up
CNC machining is seen as fast and efficient, but I’ve found that it’s slower to set up and run than manual machining.
Before you can begin machining on CNC machines, you’ll need to program each tool path and ensure the CNC mill has the correct tools equipped.
Compare that to manual machining, where you can start working after performing the necessary safety checks and once your operator gives the signal.
Manual machining provides a short turnaround and the flexibility to create unique parts, especially if you need something for quick repairs or to make prototypes.
Better for Smaller Orders
CNC machining may seem poised to take over manual mills, but manual machining remains a good option for smaller batches of parts.
While CNC machines can handle large-scale orders, manual machines can fill in smaller orders requiring simpler parts.
If setting up your CNC machine and writing the code for it would take more time than simply machining the part yourself, manual machining becomes more efficient.
Great as a Backup
CNC machines may seem better than manual mills in every way, but they can still break down. Manual machines can fill in this gap.
A purely CNC-focused engineer may have issues operating manual machines. This makes it important to ensure you still have skilled machinists who can take over.
Learning how to use both CNC and manual mills will help make your machinists more efficient and ensure you have backup options if your CNC unit malfunctions.
Skills Taught
Learning to produce parts manually is a valuable skill that is difficult to replace, even with the adoption of CNC machining.
I also recommend getting your start in manual machining and jumping to CNC once experienced.
This ensures you won’t have trouble if your CNC unit breaks down mid-order. Emergencies can occur, and it’s crucial to be able to finish your orders.
Regardless of how efficient CNC machines become, you may get an order for unique or handcrafted parts that are too difficult to program for CNC machining.
These may be too inefficient for CNC machining, so manual machining still has a place.
Disadvantages
Manual machining may be the traditional way of manufacturing parts, but it’s not perfect. Here are some reasons why CNC machining is often touted as more popular.
My discussion of CNC machining vs. manual machining isn’t complete without covering these issues.
Labor
A significant difference between CNC and manual machining is the labor required for production.
With manual machining, each machine needs to be controlled by one operator since they need to guide the workpiece to the cutting tool during operation.
This isn’t an issue with CNC machining because production is almost completely automated. A lower labor requirement can free your machinists to work on multiple machines.
Consistency
The machining process can take time for each part, and it isn’t easy to accurately reproduce the same finished part consistently with manual milling.
Tracing the same tool path hundreds or thousands of times for an order may be difficult even for highly-trained machinists and can result in a high scrap rate.
CNC machining eliminates this problem by leaving the production to software and servo motors. CNC production is precise and accurate, so you can create bulk orders without issue.
Training
Because of the risks of injury involved, manual machining should only be performed by experienced machinists or trainees under supervision.
This can significantly slow the manufacturing process if you don’t have enough operators with machining skills.
In contrast, a single operator can utilize multiple CNC mills simultaneously. The operator must ensure that the correct tools are loaded, and the tool path is programmed correctly.
What Is CNC Milling?
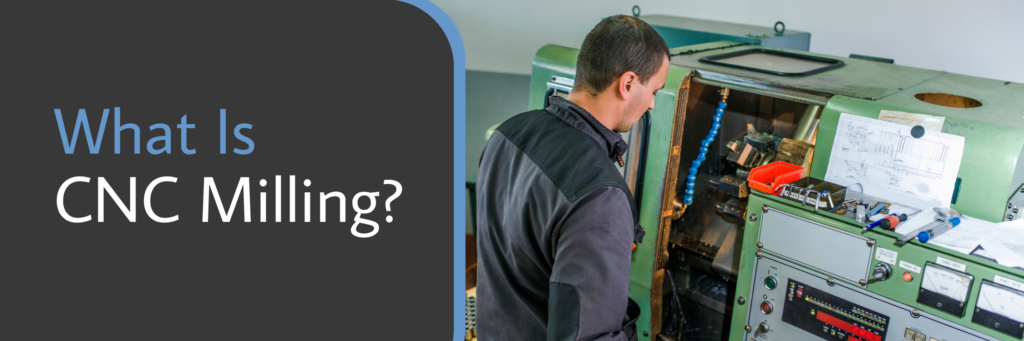
A CNC milling machine is a fusion between computer programming and machine operation. “CNC” stands for “Computer Numerical Control.”
CNC is a set of pre-programmed instructions that are input into a programmable controller and used to direct your machine’s tooling.
CNC machining relies on CAD (Computer-Aided Design) and CAM (Computer-Aided Manufacturing) to create parts. The finished workpiece’s design is first created in CAD software like Fusion360.
Like manual machining, the tooling is secured in the machine itself, but CNC machining is performed by servo motors and software, removing the potential for human error.
CNC milling machines can produce components from various materials, including metals, glass, and ceramics.
Advantages
Here are some benefits of CNC machining over manual machining.
Precision and Accuracy
CNC machines are better suited for making intricate parts with tighter tolerance requirements than manual mills because computers, instead of humans, control them.
CNC machining is designed for high-precision, high-volume manufacturing, but it wouldn’t be as popular if they weren’t accurate.
A skilled operator can match the precision of a CNC machine, but it would take more time to create a single finished workpiece.
Consistency
Some precise components are difficult to produce with a manual machine. It’s even more difficult to make them, especially if they’re more intricate consistently.
If you need to produce a large batch of the same product consistently, then a CNC mill is what you need. Since the manufacturing is controlled by software, you don’t need to worry about the milling machine getting tired like an operator.
You can achieve consistent production regardless of how long your CNC unit runs, and it only needs to stop for maintenance.
The operator doesn’t need to change the tools since some CNC machines have automatic tool changers. Just ensure you’ve programmed the machine properly.
Speed
Another weakness of manual machines is that they can only work on one plane simultaneously. This slows down production and isn’t ideal for completing large orders.
With multiple axes and cutting running on the stock at once, CNC machining can create workpieces faster.
Disadvantages
I’ve covered some of the advantages of CNC machines, but they haven’t completely replaced manual machines yet. Here are some of the hurdles you may face with CNC mills.
Computer Knowledge
While CNC mills are ideal for big projects and extensive production runs, they also require their operator to input instructions, typically written in either G-Code or M-Code.
A machinist without sufficient programming knowledge won’t be able to operate a CNC mill. This creates a barrier of entry to CNC machining that engineers must overcome.
Cost
CNC machining is more expensive than manual machining. Apart from the up-front cost of the CNC machines, you’ll also need someone with G-Code and M-Code knowledge to operate the machine.
You’ll also need a computer to interface with the CNC machine. In contrast, manual machining only requires the machine itself and an operator.
However, that’s only if you’re manufacturing smaller orders. For bulk production, CNC machining is more cost-efficient.
Worse for Smaller Orders
You can’t begin CNC machining quickly like with manual mills. You must write a program to control your tooling and ensure your unit has every required tool loaded first.
This major time commitment is efficient in the long run for larger orders but can’t match the speed of a skilled engineer who can operate a manual machine.
Maintenance
One of CNC machining’s greatest issues is the maintenance and downtime between production runs. While the machine can run almost indefinitely, it still needs to be paused for maintenance.
When this happens, all manufacturing must stop. You can only continue production once the machine’s issues have been addressed.
Even though I mentioned an operator could oversee multiple CNC units at once, they also have to be careful not to push them too hard.
Spindles, cutting tools, and ball bearings can malfunction during high-speed production, and the unit will need to be turned off for maintenance. It’ll also cost you for repairs!
Manual Milling vs. CNC Milling: Main Differences
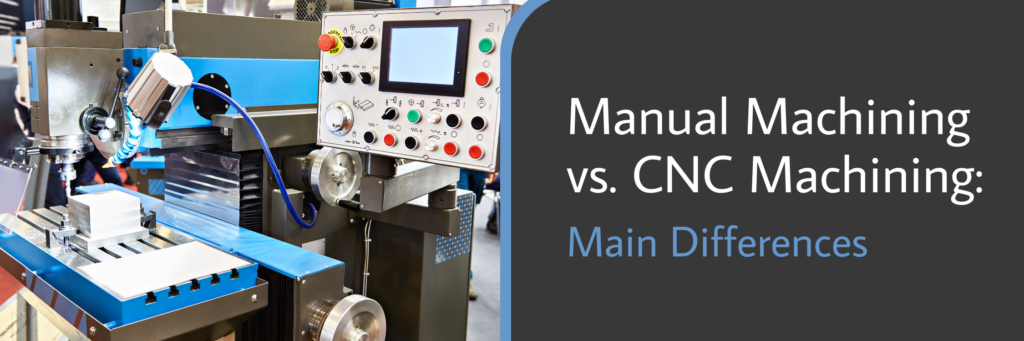
Here I’ll tackle the main differences between manual machining and CNC machining.
Safety
Machining on a manual mill requires the operator to guide the workpiece toward the cutting tool, risking injury as they operate.
Operators don’t need to place their hands in the tool path as they remove material from the stock, so there’s less risk of injury.
In contrast, CNC operation is controlled primarily by the program you feed into the CNC machine. Once the instructions are in, you can leave most of the machining process to the mill.
The tooling of CNC machines also typically happens behind guards or large enclosed chambers, so there’s less risk of your hands getting caught in the tool path.
Cost
The main difference between CNC milling machines and manual machines is their cost. CNC units are more expensive than manual mills because of all the extra components.
It would be best if you had a computer to interface with the milling machine, the production unit itself, and a trained engineer who can program it.
Compare that to a manual operator who needs the stock, the manual mill, and their knowledge. CNC units are becoming more affordable, but manual machines are still more affordable.
If you’re running a smaller workshop that won’t benefit from the large-scale production of CNC machining, get a manual milling machine instead.
Precision
CNC mills are high-precision machines designed to remove the possibility of human error from the machining process.
This leaves the CNC machinist free to operate several machines simultaneously if required, as opposed to a manual machine or lathe.
When operating a manual machine, the machinist has to focus on a single milling machine. While this is great for handcrafted pieces and prototype parts, it can’t match a computer’s precision.
Some CNC mills can detect vibration to avoid chatter when milling workpieces.
Production Time
You can’t use a manual milling machine unless you have trained in-house machinists. Even then, workers need breaks from production.
In contrast, CNC milling machines are designed for high-production runs. CNC machines can manufacture thousands of parts with less labor.
CNC machines also don’t need breaks unless they need maintenance or a cutting tool has worn out.
While this makes CNC machining more efficient, it’s also best not to depend completely on it. They can still break down mid-production.
Skills Required
A CNC milling machine and manual milling machines are both useful pieces of equipment, but they require different areas of expertise.
CNC machining requires the operator to design the finished part, program the correct tool path for the machine to follow and set up the different cutting tools.
This results in a high-precision device suited for high-volume production, but it’s different from manual machining.
You can skip production with manual machining if the operator is skilled. All they need is the milling machine and the design.
In some cases, manual machining will be faster than CNC machining if the finished part’s design is simple enough for an operator to produce.
Applications
Both manual and CNC machining have applications in various industries. Both mills can manufacture components for different industries and often support these industries.
These industries include the automotive, medical, and aerospace industries. The automotive and medical industries, in particular, often test out prototypes before moving to mass production.
Manual and CNC machines are also used to mill parts and fittings for the oil and gas industry, which have high tolerance requirements because all their components need to work as-is.
Many industries that use milled parts are government-regulated, like the defense sector.
Add the regular upgrades that military and medical equipment regularly go through, and you have lots of work for both manual and CNC workshops.
Frequently Asked Questions (FAQs)
Learn more about these essential machine shop tools here.
How Can We Differentiate Between a Manual Lathe vs. CNC Lathe?
The CNC lathe is another CNC machine that’s risen alongside its manual original. A CNC lathe can produce finished parts without a machinist’s input, like a manual lathe.
The largest differences between a manual and a CNC lathe are the control panel and foot pedals on the CNC lathe.
A CNC lathe can alter surface roughness like a manual lathe, but a CNC lathe is more accurate. Manual lathes aren’t as expensive as CNC lathes but are also slower than CNC lathes. Being able to offload your work to the lathe is the main benefit.
What Are the Three Basic Types of Milling Machines?
All mills are designed to remove material from stock, but they go about it differently and according to your workshop’s needs. Whether you’re looking at knee mills or fixed-bed mills, there are 3 general kinds.
The first is the manual machines and then the CNC units. The third is hybrids, essentially CNC units that can also be used for quick manual repairs if required.
Hybrid machines like the ProtoTRAK K3 look similar to manual mills but are programmable.
How Accurate Is CNC Machining?
A CNC machine is designed to be extremely precise and accurate thanks to its computer-assisted production. This is one of the greatest advantages of CNC machining vs. manual machining.
Precision and accuracy are about closeness and repeatability, and CNC machining offers both. Some CNC machines can produce parts with a tolerance of ±0.00508mm to ±0.0127mm.
This means if you need to create parts with exact measurements, CNC machining can do the job.
Manual Milling vs. CNC Milling: Which Is Better to Use?
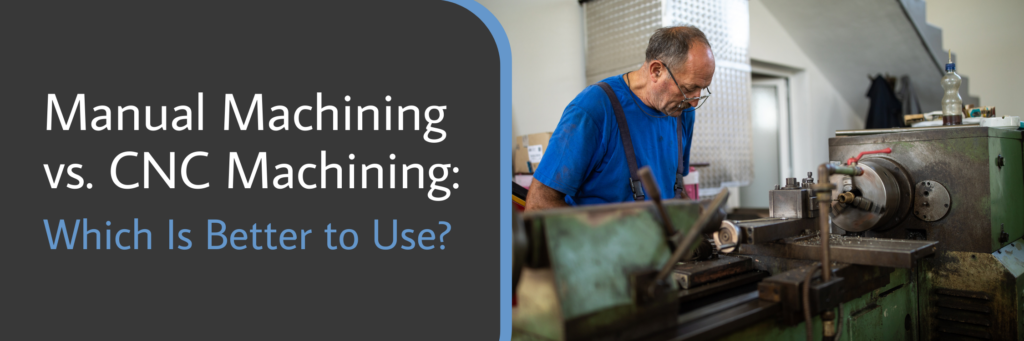
If you’re still lost on manual milling vs. CNC milling, here’s my quick guide on when to use either machine.
CNC machining vs. manual machining may seem redundant since a CNC machine outclasses its manual counterpart in every way.
But many machine shops still keep a manual mill on hand for quick repairs and emergencies. They’re also ideal for producing smaller orders or less-precise workpieces.
Use Manual Milling If:
- You don’t have time to set up a CNC machine for production
- You need to make a quick repair for one part
- You’re not familiar with G-Code and M-Code
- You’re manufacturing smaller orders
- You’re producing a prototype component
Use CNC Milling If:
- You need to produce lots of components
- Your workpieces need precise final measurements
- You have CNC engineers who know how to program
- Your machine shop has the production capacity
- Your order needs to be accomplished quickly