Disclaimer: As an Amazon affiliate, I may earn a small percentage from qualifying purchases. This is at no extra cost to you. Learn more here.
Almost every shop with machining operations has a lathe machine.
This POWERFUL tool is used for cutting, turning, forming, spinning, passivation, and other related purposes.
If you’re a beginner or haven’t encountered this cutting tool before, it might be a little confusing with all the main components.
Hence, before laying your hands on it, familiarizing yourself with the different parts of a lathe machine and its functions should be your first assignment.
In this article, I will share with you the things I know about lathe operation, its main components, and the distinct parts of lathe machines depending on your tool.
Key Takeaways:
- A lathe machine is used to rotate workpieces (wood and metal) to perform various operations, including cutting, facing, knurling, and deformation.
- Common operations in a lathe machine involve metal spinning, woodturning, metalworking, thermal spraying, forming screw threads, and creating cylindrical, circular, and flat surfaces.
- Lathe machines have distinct parts from each other depending on the type. But you’re likely to encounter 11 common components.
- Metal lathes can handle BOTH metal and wood workpieces. But, wood lathes can only be used for wood stocks.
- CNC lathes are the most modern lathes. But, the operator must be a trained professional due to its complexity.
What Are the Different Parts of a Lathe Machine?
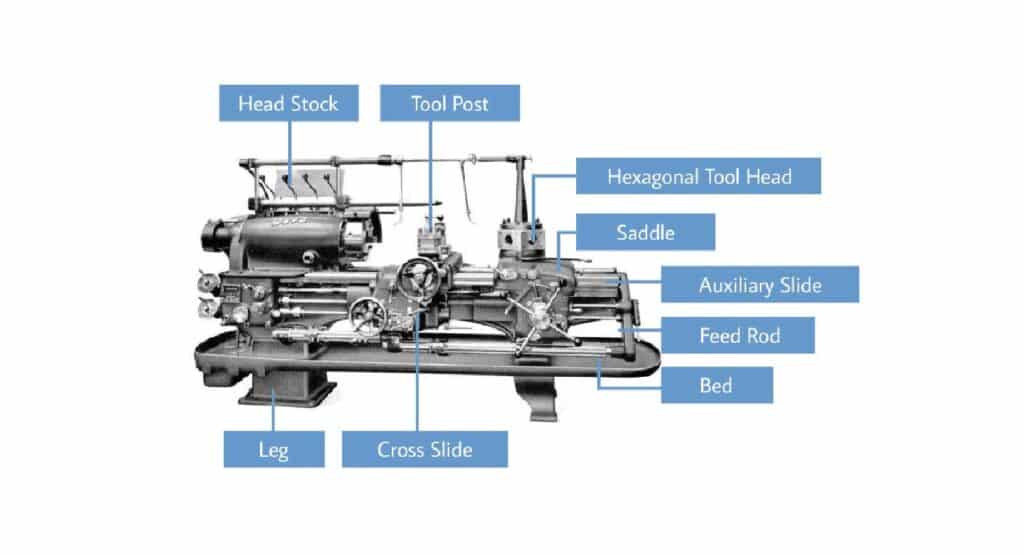
There are several parts in a lathe machine. It consists of main components that are similar to all types of lathe machines.
But, it also has parts depending on its specific use.
At first, I also struggled with getting around this machine tool. But I guarantee that studying it is NOT as hard as it sounds!
Bed
The lathe bed is the base of the machine tool.
It’s usually a cast iron structure that houses other major parts, including the headstock, spindle, tool post, tailstock, and the like.
This component is supported on broad-box columns. Its upper exterior plane can either be scraped or grounded to provide the guiding and sliding surfaces.
The size and length of the lathe bed likely indicate the MAXIMUM length of the workpiece you can process in one machining operation.
Headstock
The headstock of the lathe machine is found on the left part of the bed.
It is labeled as the POWERHOUSE of the lathe and holds several drive components, like the spindle motor, gearbox, belt drive, and other holding devices.
It also houses accessories like the three-jaw chuck, faceplate, and lathe dog.
The headstock is the component where the gear speed control levers or feed controllers are mounted.
In CNC lathe machines, the headstock is upgraded by installing a bar feeder for AUTOMATIC feed functions and continuous lathe machine operations.
This all-metal structure provides strength to the machine tool, enabling it to resist strong vibrations during a machining operation.
It also supports the main spindle and aligns it properly. Plus, it holds the necessary transmission mechanism with speed-changing levers for multiple speeds.
Tailstock
On the other hand, the tailstock is found on the opposite side of the headstock.
One of its basic functions includes providing support on the other end of the workpiece during lathe operations.
It’s also essential in holding the tools when performing a drilling operation, reaming operation, turning operation, knurling operation, and other operations in the machine.
You can find the dead centers, adjusting screws, and hand wheel on the tailstock. Its body is also adjustable on the base, which mounts the guideways.
Carriage
Between the headstocks and tailstock, you’ll be able to locate the carriage. This component guides, supports, and feeds the workpiece during various operations.
This is configured with the feed rod and houses a hand wheel to control its movement parallel to the spindle axis (Z-axis).
Apart from this, the carriage is also the part where other parts are mounted, which include:
- Saddle
- Compound rest
- Cross slide
- Tool post
- Apron
Saddle
The saddle is the small H-shaped part on top of the carriage that holds the tool post. It also supports other components, like the compound rest & cross slide.
Cross Slide
The cross slide is attached to the saddle with a female and male dovetail.
Its top surface consists of T slots, which fix the coolant attachments and rear tool post.
The cross slide provides lateral movement to the cutting tool along the X-axis, which determines the cut’s depth during the machining operation.
Compound Rest
The compound rest sits on top of the cross slide, and above it is the compound slide. It supports the tool post and cutting tool to be in various positions.
This is necessary for turning angles during a turning operation and in boring short tapers and forms in a taper turning operation.
It enables these cutting tools to perform ANGLED OPERATIONS, like chamfering and taper turning.
However, you must remember to set it at a desired shape or angle before continuing with the cutting process.
Tool Post
The tool post is where you can find the cutting tool holder for various cutting tools. This part allows the tilting tool to adjust the cutting edge’s height.
The tool holder is mounted on the cross slide. Hence, you can move it along the longitudinal or lateral axis of the lathe machine.
The combined movement, on the other hand, allows you to achieve the desired machining operation.
You can configure the tool post on a metal lathe machine into four different settings: single screw, open side, four bolt, and four-way.
Gang tool lathes, on the other hand, have special tool posts to hold multiple cutting tools for a distinct machining process.
Apron
The apron is coupled with the feed rod on the carriage for automatic movement. It’s also fastened with the saddle, hanging over the front of the bed.
This component has gears and clutches, which transmit motion from the feed rod to the carriage.
Additionally, it houses the split nut that engages with the lead screw when cutting threads.
Lead Screw
Another major component among lathe machine parts is the lead screw — a long driveshaft with acme threads.
This is usually used during a thread-cutting operation and finish taper-turning operations.
It facilitates longitudinal movement to move the carriage automatically and is used to set automatic feed.
Threading operations involve a rotating workpiece plus the linear movement of the tool. Such a rotation is achieved through the chuck, while the lead screw provides linear movement.
Feed Rod
This rod is a power transmission mechanism that enables the carriage’s precise linear movement along with the lathe machine’s longitudinal axis.
Other lathe machine tools use lead screws instead of feed rods.
Chip Pan
The chip pan is the metal tray at the bottom of the lathe machine. Its main purpose is collecting the chips produced during the machining process.
With the chip pan, you’ll minimize the hassle of collecting chips scattered on the shop floor.
Hand Wheel
Hand wheels are essential in positioning the parts of the lathe machine at the desired angle. Each component has a dedicated hand wheel that you can rotate.
An ordinary lathe machine may contain up to three hand wheels, which control the carriage, tailstock, and cutting tool.
Chuck
The chuck is a work-holding device utilized in mounting workpieces having distinct diameters.
It particularly holds those with a short length and large diameter and those with irregular shapes.
The commonly used types of chuck are as follows:
- Three-jaw or four-jaw chuck
- Collet chuck
- Magnetic chuck
But for a CNC lathe, a hydraulic chuck is used. Compared to manual chucks, this is easier to align, as it clamps the workpiece AUTOMATICALLY.
Main Spindle
The lathe spindle is the rotary component of the machine tool.
The rotating motion produced by the electric motor is passed on to the spindle, causing the chuck and workpiece to rotate alongside it.
A typical lathe machine has one spindle to do the job. But, others may have multiple spindles to enhance productivity.
Cooling System
This component is particular among metal lathe machines because metal workpieces generate frictional heat. Hence, a cooling system is needed to PREVENT damage.
The system has a tank that stores the cutting fluid and pumps it to the machining area towards the cutting area.
It lubricates and cools the medium by removing the heat from the point of contact.
Diagram of a Lathe Machine
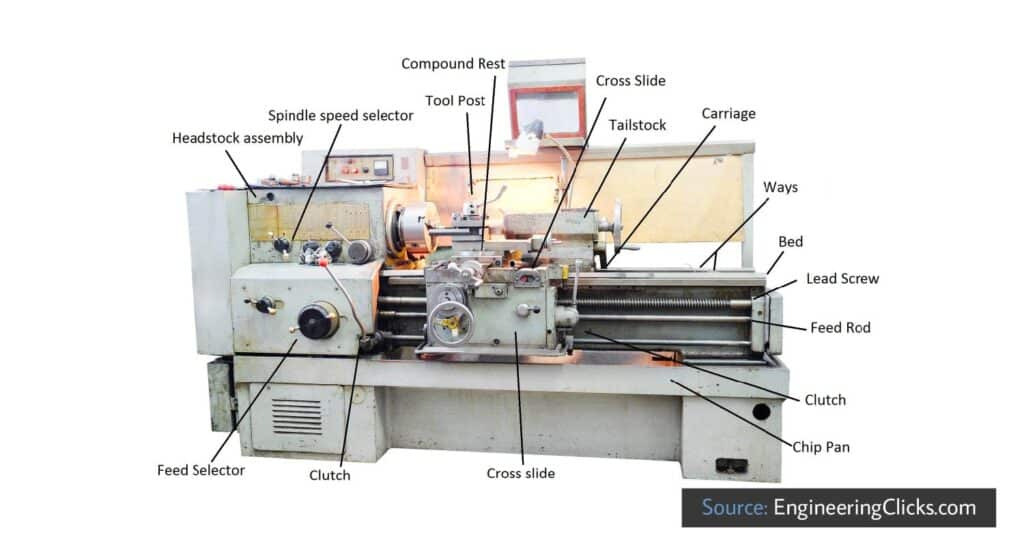
I won’t stop at knowing a lathe machine’s main function and parts. You also need to visualize the machine and see each component’s location.
I inserted a lathe diagram in this section, illustrating the parts of the machine tool. The photo above will show you the main parts mounted in the lathe machine:
Different Types of Lathe Machines
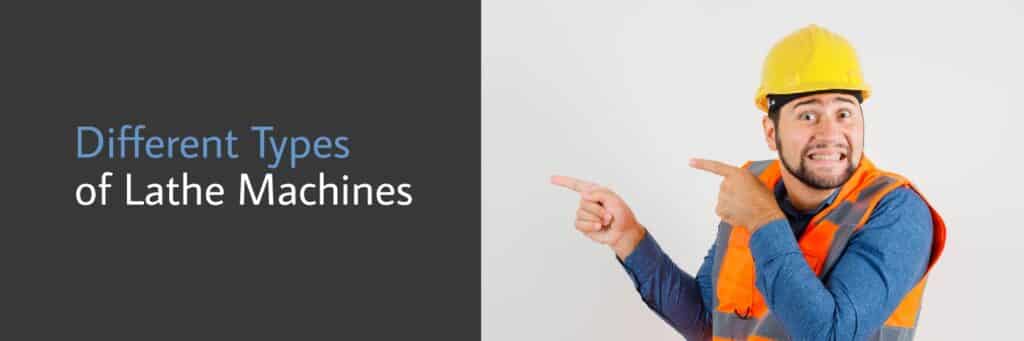
There are different types of lathe machines that are specific to their purpose and performance. These are as follows:
- Speed lathe machine
- Center lathe or engine lathe machine
- Capstan and turret lathe machine
- Toolroom lathe machine
- Bench lathe machine
- Automatic lathe machine
- Special-purpose lathe machine
- CNC lathe machine
In the next section, I’ll provide brief descriptions of the 8 types of lathe machines, plus metal and wood lathes, so you’ll know which machine to use.
Speed Lathe
A speed lathe is a hand-operated machine used by woodworkers. It provides a HIGH spindle speed from 1200 to 3600 rpm.
This type uses a light force and lesser depth in the cut compared to other lathe machine tools.
This tool is commonly used for woodturning, metal spinning, centering, and polishing.
Center Lathe or Engine Lathe
The center or engine lathe is the most popular among the other types and is used for metal or woodworking.
It’s commonly utilized as a turning, grooving, facing, thread-cutting, and knurling tool.
If you’re looking for a machine that handles pieces up to 1 meter in diameter, this lathe is the one I recommend.
Capstan Lathe and Turret Lathe
A capstan lathe and turret lathe are used for mass production. I can describe it as the older brother of an engine lathe because it is more UPGRADED.
The tailstock on this tool is replaced with hexagonal turret heads, and it’s mounted with THREE instead of one tool holder.
You can also install different tools in this machine, may it be for a drilling operation, knurling operation, or other purposes.
Hence, you can perform MULTIPLE tasks in a short time.
Learn more about the difference between capstan lathe and turret lathe.
Tool Room Lathe
This is the machine you’ll most likely encounter if your projects involve making precision parts, including gauges, jigs, and fixtures.
A tool room works at multiple speeds, from the lowest to a quite higher 2500 rpm.
Bench Lathe
A bench lathe is used for very small precision projects. Jewelers and watchmakers are the ones who commonly use this tool.
It performs similar tasks as an engine lathe and consists of similar parts.
Automatic Lathe
An automatic lathe is a machine capable of automatically feeding cutting tools due to its mechanisms.
It can control 5 to 6 lathes at a time, and it performs quickly and does really well in heavy-duty production.
Special-Purpose Lathe
Special-purpose lathes are custom-made to perform specific tasks and production work. These are commonly utilized in heavy-duty projects regular lathes can’t perform.
Examples of these are:
- Gap bed
- Missile
- Hydraulic quill
- Duplex
- Crankshaft
Metal Lathe
A metal lathe is used in machining hard metal workpieces like iron and steel. Yet, you can also use it to process wood.
As you noticed, the types of lathes I specified in the previous sections support both mediums.
By using this, you can deform a workpiece to achieve your desired shape.
CNC Lathe
A CNC lathe is the most updated type of lathe machine discussed in this article. CNC machines are integrated with modern computer numeric control systems (CNC).
These systems allow users to add a CAD/CAM program to command the machine. In turn, the CNC lathe automatically operates according to the input.
CNC lathes are SPEEDY and more HEAVY-DUTY. Its accuracy and precision are also better compared to manually-operated machines.
Mass production with a CNC lathe is cheaper and relatively faster, too.
But, CNC lathes are costly.
You may need to shell out lots of cash for CNC lathes’ power consumption and routine maintenance, plus you must hire a professional to operate this.
NOTE: CNC lathes are more complex than other machines. No one should operate CNC lathes without proper training and skill.
Wood Lathe
Wood lathes can only work with wood-based workpieces. It’s mainly used to cut, drill, sand, face, and deform such materials.
You can move the tool against the workpiece to remove material and achieve your intended shape and size.
Frequently Asked Questions
Let’s go through some common questions you might have in mind:
Can You Use CNC Lathe on Wood?
ABSOLUTELY! You can use both metal and wood workpieces in CNC lathes.
However, if the wood stock is oddly irregular in structure, I suggest you use hand-held machines, which can handle vibrations better than a CNC lathe.
What Are Important Terms to Know in Using a Lathe Machine?
SOB and DBC are important terms to remember when using a lathe.
SOB (Swing Over Bed)
SOB refers to the maximum workpiece diameter a machine can handle. Generally, this is twice the distance between the bed and the center of the spindle.
DBC (Distance Between Centers)
DBC, on the other hand, refers to the distance between the headstock and tailstock.
This is equal to the bed’s length, which determines the maximum workpiece length you can turn on the machine.
Conclusion
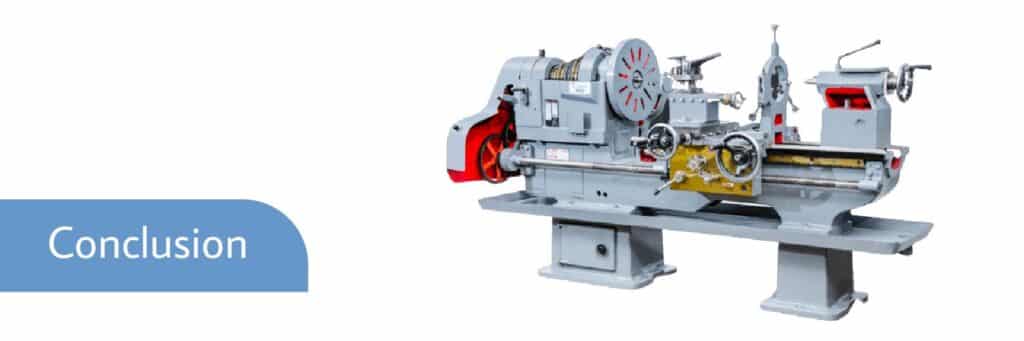
There are different parts of the lathe you MUST familiarize yourself with before getting your hands on one.
It may be confusing at first, but I guarantee you’ll get the hang of it in the long run.
I experienced the same dilemma as you when I was only a beginner. Yet, enduring the painful process of learning the basics is totally WORTH IT.
I hope this guide was able to help you in your lathe learning journey!