Disclaimer: As an Amazon affiliate, I may earn a small percentage from qualifying purchases. This is at no extra cost to you. Learn more here.
Last Updated on March 1, 2023 by Charles Wilson
For over 200 years, milling machines have provided many workers with a lot of aid in cutting metal and even wood.
In fact, this heavy-duty cutting tool has become an essential piece of equipment that many workers can’t live without anymore. Furthermore, it has helped the manufacturing industry thrive.
Today, I’ll talk to you about the different milling machine parts, the machining process, and the types of milling machines you can find.
Key Takeaways
A good milling cutter can easily go through metal and wood without resistance.
Milling machines have up to ten vital parts for their operation.
There are different types of milling machines depending on the project you need to do.
Observing the standard safety operating procedures when using a milling machine is vital.
What Are Milling Machines?
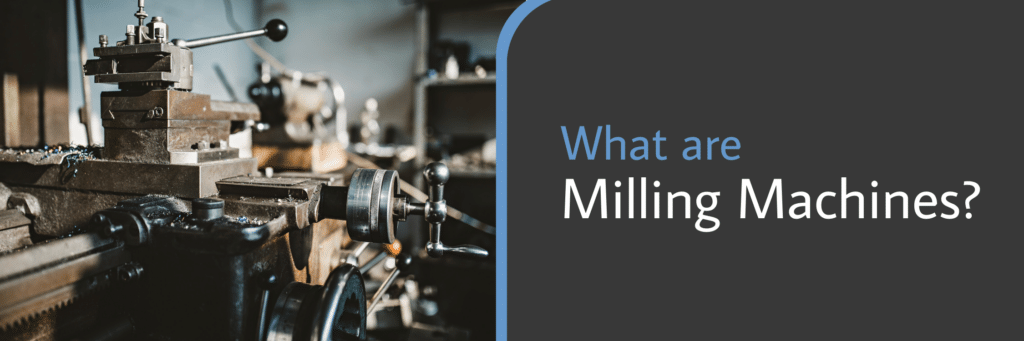
Milling machines look very intimidating.
They’re huge and clanky, with many different parts sticking out everywhere. The rotating milling cutter is just enough to give you the chills just thinking of how sharp it is.
But don’t be fooled because milling machines aren’t at all that intimidating. Behind its tough exterior, milling machines are easy to operate and get the hang of.
In the 1800s, milling machines were used only for simple clock-working and gun-making.
As the years progressed, milling machines underwent many changes and innovations to make them one of the must-have tools in the manufacturing industry.
For most people, a milling machine can be best described as a fancy metal cutting tool. All you have to do is put in your work and let the rotating multipoint cutter do the job.
But anyone using milling machines for years knows the work doesn’t end there.
Generally, a milling machine can cut through heavy metal, regardless of its shape and dimension, at high speeds and accuracy.
Just imagine how sharp the blade is to perform such a function!
IMPORTANT NOTE: Do not wear loose clothing or accessories when operating a milling machine. Always observe the necessary safety precautions, such as wearing safety goggles and sturdy footwear.
What Are the Different Parts of a Milling Machine?
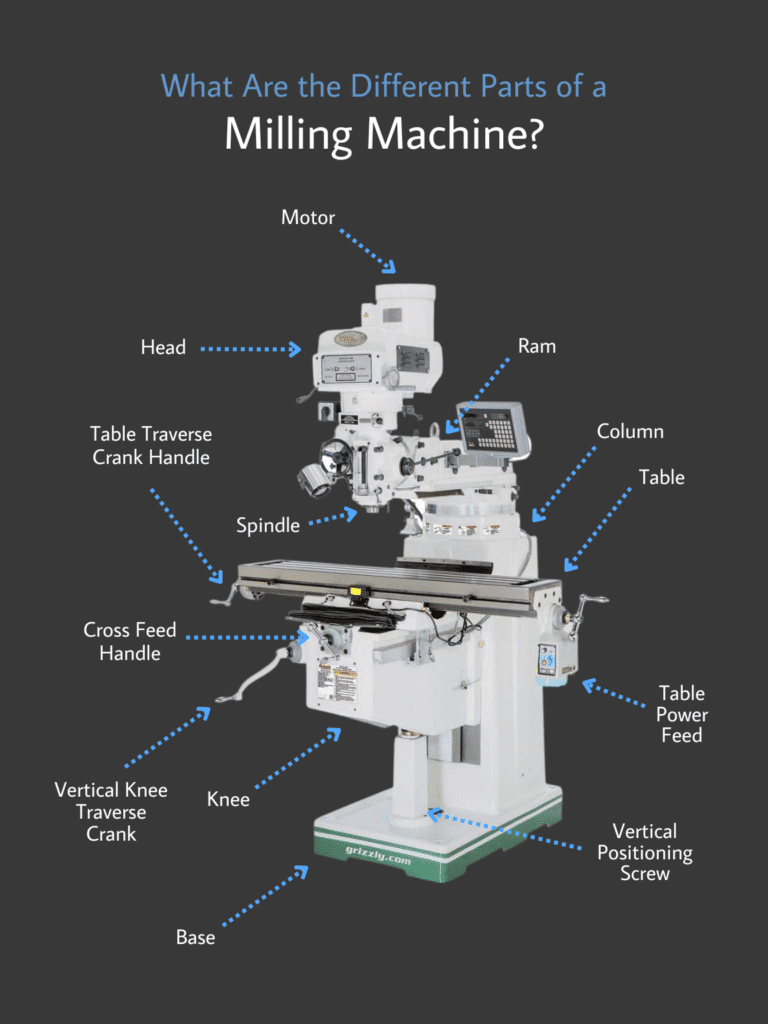
There’s more to a milling machine than the milling head and milling cutters.
It is best to understand what a milling machine is and how it works by breaking it down and discussing its different parts.
I’ve listed down some of the main parts of the milling machine you need to know about.
We’ll go through each of them for you to understand how their role helps in the milling operation.
Remember that you should never attempt to remove any parts of the milling machine without professional assistance.
1) Base
One of the most crucial parts of a milling machine is the base because it holds and supports the entire machine together.
Many people don’t always pay close attention to the base of a milling machine — but they should.
In general, the base of a good milling machine should always be made of cast iron. Cast irons have a hard exterior that can withstand any operation.
2) Column
The column always sits vertically on top of the base. It is responsible for the milling operation because it houses the motor and powers the spindle.
First-timers need to get acquainted with the different controls found on the column of a milling machine.
PRO TIP: Keeping the oil and coolant reservoir full helps the spindle have a smooth and continuous operation.
3) Spindle
A vertical milling machine can never operate the way that it does without the spindle.
The spindle is responsible for holding a piece of work on the table and powering the cutting tools. Looking closely at the spindle, you’d notice an internal taper machined on it.
Spindles are typically powered by the motor inside the column of the milling machine.
4) Knee, Saddle, and Work Table
These three parts of the milling machine always go hand in hand.
Let me begin with the knee. The knee in a milling machine plays a vital role because it supports both the saddle and the table.
It also houses some motors and controls to help operate the milling machine.
You should never attempt to adjust the knee manually. Instead, use a vertical positioning screw or elevating screw. An elevating screw can help raise or lower the knee.
Resting on top of the knee is the saddle, which also supports the table.
And finally, the table sits on top of the saddle. This is the most vital part of the three because it is where most of the work gets done.
Work tables can be operated either manually or automatically. Regardless, a mark of a good work table is if it can hold the material (e.g.piece of metal) down tightly.
5) Milling Cutter
Milling cutters are the main event when it comes to milling operations. As its name suggests, a milling cutter is responsible for cutting hard and heavy materials.
These days, it’s not enough that milling cutters can cut. Instead, many people are also interested in finding out how well their milling cutter can perform and how to utilize them.
The more versatile it is, the better.
Always ensure that your milling cutters are sharp to prevent flaws or problems in your workpiece. More importantly, keep body parts away from a revolving cutter.
6) Overarm
The overarm can often be found on the column of horizontal milling machines. It is usually a horizontal beam that supports the spindle in operation.
7) Arbor Supports
Arbor supports help hold down the material in place and the outer end of the harbor.
During operations, the arbor support ensures that the outer end won’t spring out of place.
You can find two types of arbor support. The first type has a small diameter bearing hole of only one inch, while the other has a 24-inch large diameter bearing hole.
An arbor support is present only in a horizontal milling machine.
8) Power Feed Mechanism
If you’ve always wondered how metals are cut into distinct shapes and designs, it’s all thanks to the power feed mechanism.
The beauty of power feed mechanisms is their ability to configure how you want your metal pieces or tools to come out.
You can shape your tools and metal to the desired shape you’ve always wanted.
To make the most of this part, check for the rapid traverse lever on the power feed mechanism.
Types of Milling Machines
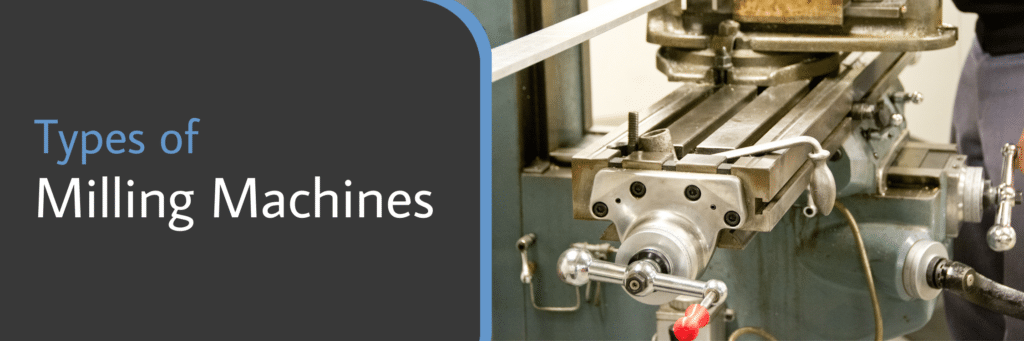
There are so many different milling machines out there that I sometimes still find it challenging to remember how each type differs!
Below, I’ve listed down some common types of milling machines you would encounter.
1) Horizontal Milling Machine
Horizontal milling machines are popular for being one of the sturdiest and most reliable milling machines out there.
The spindle on a horizontal milling machine is always set on a horizontal axis position. Thanks to its axis orientation, a horizontal milling machine can move either in a longitude, vertical, or crosswise direction.
On average, a horizontal milling machine is great to have around the workplace because it’s good for many types of milling machine operations in the manufacturing industry.
2) Vertical Milling Machine
Vertical milling machines are usually distinguished by the location of the spindle. As its name suggests, the spindle is placed in a vertical position and spins on a vertical axis.
The beauty of using vertical milling machines is that it allows for performance flexibility and precision.
Cutting grooves, faces, and slots is much easier with a vertical milling machine.
You can maximize your vertical milling machine by checking if you can use it with a vertical milling attachment or accessory.
3) Universal Milling Machine
If you’re looking for a milling machine that can do almost everything, a universal milling machine comes first on the list.
What makes the universal milling machines stand out is the table. It can pivot up to 45 degrees from its original position, making cutting grooves and slots much easier.
4) Ram Type Milling Machine
A ram-type milling machine generally sports a moveable housing where the spindle is mounted.
This milling machine can guarantee exceptional performance each time, regardless of the working load.
However, a ram-type milling machine is usually used as a vertical milling machine.
5) Surface Milling Machine
When it comes to productivity, a surface milling machine is the best because it can do a multitude of jobs.
A surface milling machine is commonly used to create smooth finishes and textures on a flat surface.
6) Thread Milling Machine
The first thing that probably pops into your head when you read “thread milling machine” is the exercise equipment.
Let me tell you now that the thread milling machine in this list differs from the exercise equipment.
Instead, a thread milling machine is commonly used for cutting and creating threads. With the help of single or several thread milling cutters, you can make several threads simultaneously.
7) Gear Milling Machine
Ever wondered how the small gears on your screws and bolts are made? The answer to that is through the use of gear milling machines.
As its name suggests, a gear milling machine creates gears of various shapes and sizes.
A gear milling machine is able to cut each piece of work based on a specific standard.
8) CNC Milling Machine
A CNC milling machine is the future of milling operation and the milling process.
CNC is “Computerized Numerical Control,” which means the whole milling operation is computerized.
CNC milling machines are favored by many people these days because they provide a ton of accuracy and precision.
All you have to do is set the exact specifications, and the machine will do the work for you.
9) Tracer-Controlled Milling Machine
As its name suggests, a tracer-controlled milling machine traces or copies any irregular surfaces or shapes.
It can then duplicate what is traced in 2D or 5D, ensuring that each work is exactly like the original.
Different Milling Machine Operations
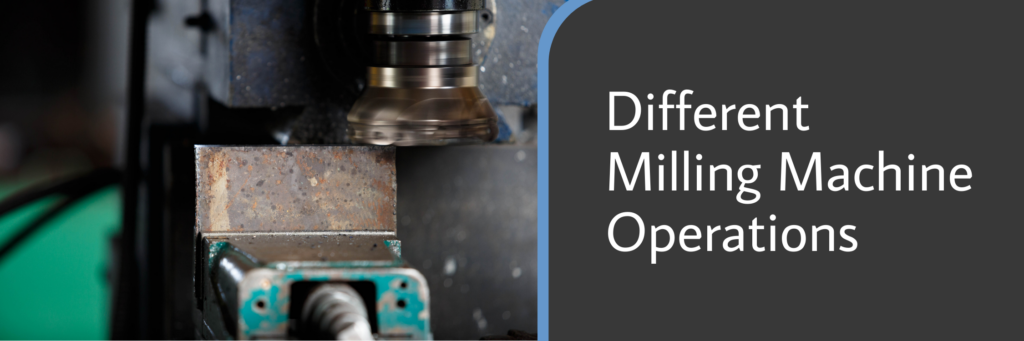
Besides having different types of milling machines, there are also different types of milling machine operations to consider.
Starting to feel confused with all the differences? Don’t worry because I’ve listed some of the different types of milling machine operations below.
1) Face Milling
Face milling is commonly used to create a flat surface on the piece of work using a face milling cutter. During the whole milling operation, only the top part of the tool is used.
How it works is that the milling machine is perpendicular to the piece of work being created, with the face milling cutter mounted on the arbor.
2) Side Milling
Side milling is almost the same as a face milling operation. The only difference is that side milling produces a flat vertical surface and is smoothed using a side milling cutter.
The type of side milling cutter to use usually depends on the type of work to be done. This way, the milling machine can accurately polish the grooves or the shape of the piece of work.
3) Plain Milling or Slab Milling
Plain milling and slab milling are the same. Plain milling is often described as a piece of work being laid parallel to the cutting tools to create flat surfaces.
A plain milling cutter creates a smooth, horizontal, and flat surface.
4) Straddle Milling
A straddle milling operation involves the use of two cutting tools. The milling cutters are placed parallel to each other, with a predetermined distance in between.
Straddle milling operations are used to work on two opposite sides of a piece of work.
5) Angle Milling/ Angular Milling
Angle milling produces the same results as creating flat surfaces. The only difference is that angular milling doesn’t deal with parallel and perpendicular flat surfaces.
With the help of a single-angle milling cutter, you can have flat vertical surfaces in no time. It can get tricky, but a sharp angular milling cutter helps in the process.
6) Gang Milling
When it comes to simultaneous cutting operations, gang milling is key.
The great thing about gang milling is that more than one milling cutter can be used to work on different operations simultaneously.
7) Form Milling
The beauty of a form milling machine is that it speeds up the entire machining process by molding or cutting the metal to the target shape.
It no longer requires manual operation — which we all know takes some time. Just imagine manually measuring and molding each metal by hand!
Corner rounding milling cutters are often used for form milling operations.
8) Saw Milling
Creating slots and holes on a piece of work is made possible with a saw milling cutter.
A great example would be cutting holes in chairs or tables for specific sizes of screws.
9) Helical Milling
An alternative to saw milling is helical milling, where a hole is cut through the work.
Helical milling is ideal for creating objects with a helical design, like helical gears and screws. Having the right proportion for each ensures the screws and helical gears remain snug inside.
10) Cam Milling
Cam milling is an important machining process that deals with creating cams.
Cams are a vital component for the opening and closing of engine valves. Believe it or not, cams can have a significant impact on the performance of an engine.
Frequently Asked Questions
There’s a lot of confusion about a milling machine and how it works.
To help you understand milling machines better, I’ve answered some of the frequently asked questions on milling machines:
What’s the Difference Between Up Milling and Down Milling?
Make no mistake in thinking that up and down milling is the same. There are several differences between the two, and knowing what they are can be crucial.
As to applicability, an up-milling machine is used for metals like brass, bronze, cast irons, and steel. On the other hand, a down milling machine is used for metals like aluminum.
The direction of the cutter for up-milling is always against the direction of the feed. Whereas in down milling, it is always with the direction.
Finally, up-milling generally requires more cutting force than down-milling.
Between the two, several people prefer down milling because of its simpler process and better finish.
What Are the 3 Types of Mills?
Overall, there are three types of milling machines you need to know about:
- Manufacturing type milling machine – Manufacturing or bed types of milling machines have a bed already permanently fixed to the machine. This provides better stability compared to any different milling machine operation.
- Planer type milling machine – This is probably the best of all milling machines, thanks to its massive size and build. When it comes to performing heavy-duty tasks, a planer-type milling machine operation will do the trick.
- Column and knee type milling machine – The column and knee type milling machine is the most common of the three I’ve mentioned. A knee and column milling machine has all the gears you need to rotate the piece of work and simply move it up or down.
What Are the 5-Axis in Milling?
The 5-axis refers to the A, B, X, Y, and Z axes.
A 5-axis milling machine can move in five different directions. This machine tool is ideal for anyone who wants more flexibility and functionality in milling machine operation.
You no longer have to remove and rotate your piece of work manually.
This means it’s a lot safer for everyone since the milling cutter can go on different sides if necessary.
The X, Y, and Z axes allow the work to move in different directions. In comparison, the A and B axes are responsible for rotating your work during operations.
Conclusion
Milling machines undoubtedly add a lot of convenience to people’s lives. Imagine what we’ll all look like if milling machines weren’t invented!
There’s more to be said about the parts of the milling machine.
But today, we’ve already covered the basics of the many parts of a milling machine, types of milling machines, and types of milling machine operations.