Disclaimer: As an Amazon affiliate, I may earn a small percentage from qualifying purchases. This is at no extra cost to you. Learn more here.
Last Updated on February 28, 2023 by Charles Wilson
One of a machinist’s most versatile tools is the knee mill, and it’s amazing how many operations they can carry out on a workpiece.
The idea behind it emerged in 1936 when Rudolph Bannow’s company produced a vertical mill with a knee and column, a rotating turret, and a sliding ram head.
Of all machine tools, these apparatuses may be the most adaptable.
It can create almost any orthogonal item, size permitting, especially when operated by an experienced machinist.
It is still a favorite among many producers. Now let’s look at this full guide I have compiled for you to know how it works and more info!
Key Takeaways
- Knee Type Machines come in both vertical and horizontal varieties. These apparatuses are employed for many plate production tasks, while horizontal devices require fewer plates.
- A Bridgeport has the rigidity and power to be a milling machine and a variable speed head with quill movement for drilling, tapping, and reaming operations. Over 370,000 units of the Bridgeport Series I have been produced over the past 70 years, making it the most popular machine ever produced.
- CNC knee mills set the new benchmark for the machining industry in terms of usability, versatility, and dependability. A CNC mill works effectively in tool rooms and job shops for small and medium production runs, prototypes, or one-off items.
- The most durable apparatuses are made with hardened and ground ways that also employ a Turcite layer for lubricity.
What Are Knee Mills?
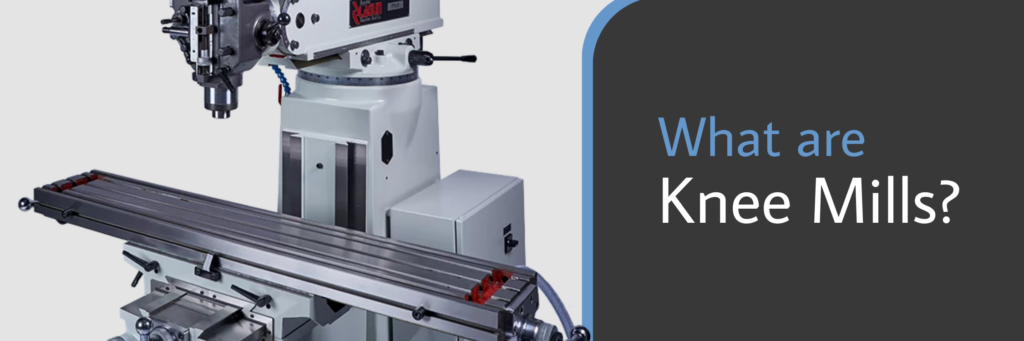
The knee mill is a versatile machine tool, sometimes called a variable-speed machine, that removes material from an object using instruments, including end mills and face mills.
This tool is an excellent place to start when addressing the widening skills gap between retiring shop veterans and the new generation that has to be trained to take their place.
While the object is clamped to a horizontal worktable or held in a secured vice for slashing, these instruments are held vertically.
Depending on the object’s height, the operator can manually raise or lower the counter.
The “knee” is a heavy-duty Meehanite casting that supports the worktable and sits vertically on a dovetail on the machine’s “column.”
The manual mill’s ability to be utilized as a drill press contributes to its adaptability.
The vertical quill, a portion of the spindle motor that moves vertically, serving as a second Z-axis, is a special feature of this machine that makes drilling possible.
A manual handle or an automatic quill feed controls quill travel.
Another benefit of these devices is that they are relatively simple and take up considerably less room than their bulkier cousins, horizontal mills.
And those pits or that keyway will be placed precisely if the manual knee mills have Acu-Rite digital readout (DRO).
Today, most vertical milling machines include a power feed which speeds up and simplifies many milling operations.
Moreover, drilling tiny pits or milling narrow slots is possible at high spindle speed without worrying about cutter breakage.
The machine spindle’s cutter head is coupled to a moveable ram that goes in and out and swivels for wider part coverage, so you may also operate on larger workpieces.
On various machines, the worktable is either hand-cranked or powered, depending on which is faster, while the saddle and knee are both moved manually.
I have realized how essential manual knee mills are to the normal machine shop when considering all the little tasks a machinist can perform.
How Does a Knee Mill Work?
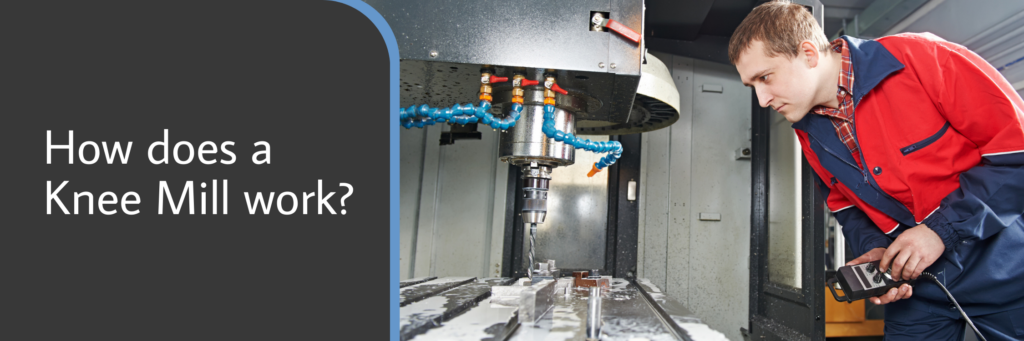
Still, no one can deny the advantages the manual knee mill offers the typical machine or fabrication company.
For instance, clamping a block to the knee mill’s table, drilling and tapping a few pits, or clamping a shaft in a vise and milling a keyway into the end takes only a few seconds.
In these situations, laborious programming is not necessary. And those holes or that keyway will be placed precisely if your manual knee mill has an Acu-Rite digital readout (DRO).
I believe that all machines operate and form metal in the same way.
A machine operates in complete contrast to a wood or metal lathe and spins the object rapidly while using a stationary machine tool to cut it.
The object is held still and secured to the counter in this position while milling tools spin at extremely high revolutions to create precise cuts.
The methods used to move the workpiece’s position are often where machine types differ.
A knee mill, like the majority of machines, can carry out a staggering array of cutting and shaping operations. These procedures include slot machining, cutting, and surfacing.
The use of milling tools, which resemble drill bits in many ways, allows for a wide variety of shaping capabilities.
These metalworking tools exist in a wide range of sizes and shapes; when employed, each one may cut shapes of various sizes.
For cutting larger things, the machine can be quite helpful. A rotating spindle may not always produce enough torque to drill holes (also known as boring.)
This configuration significantly increases the torque, enabling boring through harder materials.
The table’s ability to move vertically creates another advantage because it increases the height to which larger things can be processed.
What Is a Knee Mill Used For?
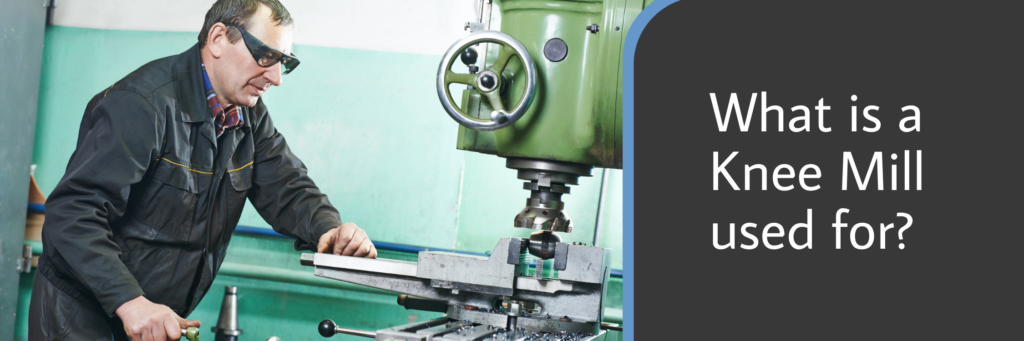
With the help of a vertical knee mill, a machinist may do various jobs, such as face milling, slotting, and boring.
Manual knee mills are excellent for prototype, tool room work, repairs, general job shop work, and R&D work.
Long workpieces can be milled and drilled, fixtures can be made, small rework can be done, and one-and-done items can be finished, depending on the knee mill’s counter size.
A machinist can go on the manual knee mill and work on a secondary operation, a repair job, or any variety of relatively modest operations while a long run is on the knee mill.
The same is true if manual lathes are present in a shop.
The R8 spindle taper of the manual knee mill contributes to its adaptability.
You can easily switch between tools for cutting a flat surface, adding a few slots, and drilling and tapping a hole in a product using an R8 collet as a machine tool holder.
The machine doesn’t require programming or tooling setup for simple machining operations.
The additional coverage provided by the movable ram allows the machine to assist in machining larger objects.
The Benefit of a Moving Table
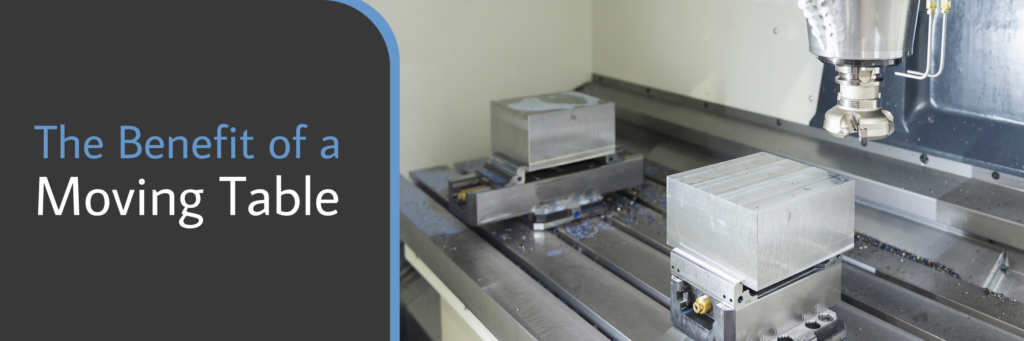
A knee milling machine is a form of standing machine that is rather straightforward. It can move along the vertical Y-axis and the horizontal X-axis.
In other words, the worktable travels along the machining axis exactly like the workpiece itself.
Bridgeport mills are another name for knee mills on occasion.
The knee mill is an adaptable machine tool ideal for various processes and workpiece types.
The presence of a worktable that can be adjusted vertically is, as was already noted, the most distinctive aspect of these apparatuses.
The worktable is supported by a knee-supported saddle, as the name suggests. The knee acts as a huge, supporting casting.
The knee’s primary purpose is to stabilize an upright machine by resting vertically on the column. Also, it may firmly and rigidly clamp the column in a set position.
It is done to fix the milling top and spindle in an upright position while working.
Flexible and Trustworthy
In current devices, the spindle is mounted vertically, e.g., parallel to the column face. The concept is intended to enable a full dome swivel on angled surfaces.
Cutting is more precise and mobile thanks to the turret and swivel dome assembly (sometimes, an object needs to be rotated 360° on the base).
When making angular cuts, the head’s position allows for greater precision when cutting along a horizontal plane.
Knee milling machines have been one of the most widely used manufacturing tools in recent years due to their adaptability and stability.
The synopsis above only scratches the surface of its capabilities.
Why Is It Still So Well-Liked?
These devices are still machine shops’ most frequently used mechanical devices.
The machine’s open design is simply beloved by machinists since it enables quick setups for straightforward tasks.
Place the workpiece into the mill, drill a few holes, or tap a few things, and the item is finished.
Also, the turret, movable ram, and tiltable head provide a very adaptable design for its work envelope. The machine’s adaptability and flexible work envelope make it useful.
The Simplicity of Use
Anyone who receives the proper education may operate this manual mill very easily. For those new to the machining sector, it is frequently the greatest place to start.
You don’t need to create intricate tooling programs or write code. Attach a drill or endmill to the collet, and you’re ready to go.
It is why machinists and metalworking enthusiasts worldwide continue to love the knee mill as one of their go-to machine devices.
Applications for Knee Mills
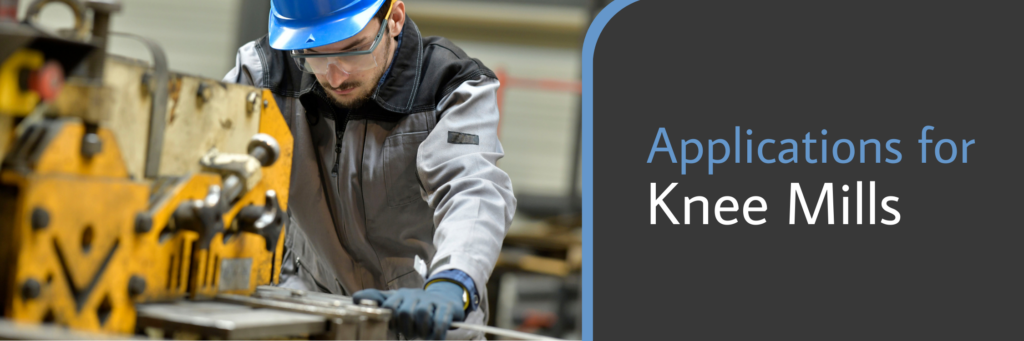
A knee mill can perform various cutting and shaping processes.
The only restriction on the size of the workpiece is the knee travel. These methods include slot machining, cutting, and surfacing.
Like drill bits, milling tools are also responsible for enabling a broad range of shaping capabilities.
These metalworking tools exist in a wide range of sizes and shapes; when employed, each one may cut shapes of various sizes. For cutting larger things, the machine can be quite helpful.
A rotating spindle may not always produce enough torque to bore (also known as a drill) holes.
By using this configuration, the torque is significantly increased, enabling drilling through tough materials.
The table’s ability to move vertically creates another advantage for the machine because it increases the height to which larger things can be processed.
Knee Mill vs. Bed Mill
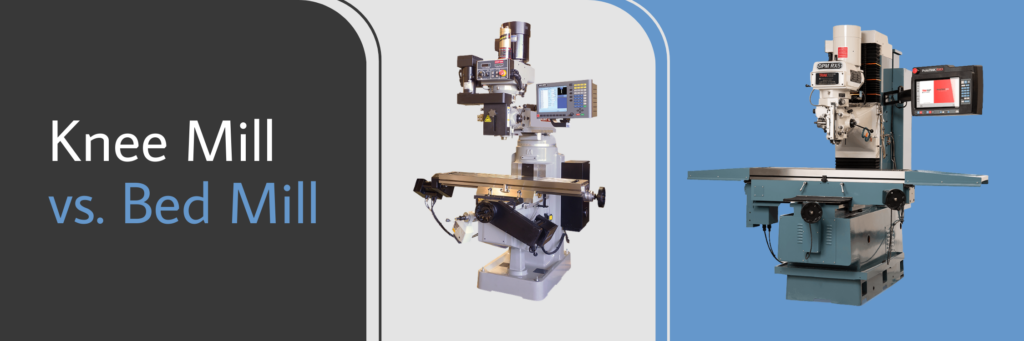
At the risk of seeming redundant, the flexibility that a knee mill offers over a bed mill is its main advantage.
Mechanically speaking, the spindle of the bed machine moves up and down, whereas the table of the knee mill moves up and down on the Z-axis.
As was already noted, a “quill” on a knee mill functions as a second Z-axis and converts the upright machine into a drill press.
With the help of a handle on the spindle head or an optional power feed, the spinning quill can be raised and lowered. Bed mills cannot perform as many tasks as these mills.
Here are a few examples:
Even though it’s never simple, using a knee mill makes it possible to manufacture larger components than a machine’s journey without moving the workpiece.
On a knee mill, you might be able to swivel the head, stretch the ram, and access inaccessible places with a bed machine.
On a knee mill, tilting the top to cut an angle into a workpiece is commonplace.
You must arrange the workpiece at the proper angle on a bed mill to achieve the same cut, which may require expensive fixtures or a challenging setup.
To drill or mill long components, you can fasten them to an angle plate and dangle them off the side of the knee mill’s table.
You can reach beyond the table by swaying the top and extending the ram.
If your bed mill has enough Z-travel to clear the piece, you must mount the part to a tall angle plate to process the end.
Although these devices have more abilities than bed machines, a bed mill can be more appropriate if you need to make a lot of heavy cuts while using maximum horsepower.
Traditional Knee Mill vs. CNC Knee Mill
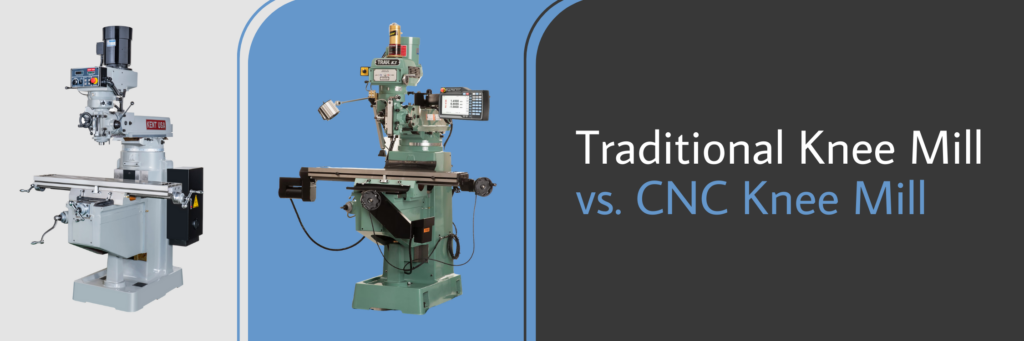
Even though both can perform standing machining, one of the main distinctions between a CNC mill and a manual milling cutter is the number of people required.
The CNC mill requires less involvement than traditional knee mills, and a skilled CNC machinist may manage multiple devices simultaneously.
The most definite benefit of a CNC knee mill, though there are others, is the decrease in labor expenses.
A CNC knee mill will repeatedly create parts that adhere to the strictest criteria once configured, allowing a computer to control its motion.
Because of one crucial component, human error, manual devices struggle to produce consistent outcomes.
Because of this, many device shops that only use manual devices experience quality problems.
In terms of production work, a CNC knee mill is the winner. A CNC knee mill can quickly produce hundreds of identical parts within predetermined tolerances.
Production can be increased beyond what manual devices can do with faster table feeds, automatic tool swaps, and box ways on a CNC machine.
It is possible to easily transition from one component to another because running the following parts on a CNC knee mill mostly involves reprogramming, replacing inserts on the milling cutter, and adding coolant.
Because complex setups, fixtures, and jigs are not required, tooling costs can be reduced, and the prototype can be finished considerably faster.
CNC shops are safer despite operating faster and machining parts faster than Bridgeport-style devices.
CNC machining frequently occurs behind a guard or a closed, transparent door to reduce the risk of injury.
There is almost no potential for workers to get their hands near moving CNC machines.
Why a CNC knee mill?
- Simple CNC operation or walk-up manual/DRO operation
- CNC mill can easily machine holes, curves, islands, and pockets.
- Streamline setup procedures and CNC machining errors
- CNC has less tooling required for better parts and finishes
- CNC will enhance the capacity and output of your current workforce
- CNC machining produces little to no waste
DID YOU KNOW? KTM-5VKF-E CNC from Kent USA weighs in at 3900 lbs., significantly heavier than other knee mills in this size range. Kent USA also showcased the first AC-Frequency drive top on a Kent USA knee mill to the general machine tool public. Kent USA has also eliminated the standard Acme or 60-degree leadscrews.
How to Pick the Best Milling Machine
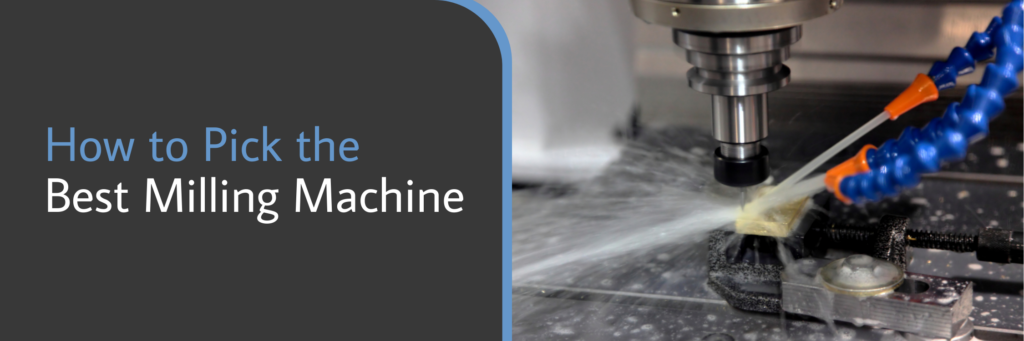
There will always be standing milling on the floor, no matter how advanced the machine shop is or how many CNC machines it owns and uses.
That’s because shops frequently buy these devices as their first machine.
After all, they are the equipment of choice for prototyping, secondary operations, and tooling and fixture work.
They are adaptable and simple to use, and a skilled machinist can produce almost anything on one.
Your business might be a startup. Perhaps you’re thinking about getting another machine to expand the capacity of your current machinery.
In either case, there are a few characteristics you ought to search for in a new device:
1) Weight and Travel Restrictions
Getting a larger machine than you require is a waste of money. The worst case scenario is having to no-quote a work due to axis travel limitations or machine load limits.
Before investing, carefully analyze your needs. It’s okay to go a little overboard in this situation.
2) Taper and Spindle Speed
The typical spindle taper on almost all knee mills is R-8. Consider using an NMTB-30 spindle for tougher cuts.
Choose a variable-speed spindle and power drawbar unless you enjoy sore arms. A 6,000-rpm spindle speed is also good if you use many small cutting tools.
3) Power Feed
The quill (the component of the machine that travels up and down) and axes have power feeds, which further lessen operator fatigue.
Also, they contribute to longer tool lives and better part quality.
4) DROs for Knee Mills
It could sound enticing to have a computerized readout. Up until the point at which you forget how many times you’ve cranked the handle and thrown away a significant piece of work.
For the best functionality, look for a DRO with memory functions, hole patterns, centerline computation, and other features. You’ll be happy that you did.
5) Coolant and Lubricant
The majority of devices offer automatic or one-shot lubrication. Make sure yours does, too.
You’ll also require a method for lubricating and cooling the product. Although a spray mist unit works, it’s not enjoyable to breathe that stuff all day.
If one is available, it is preferable to use a simple flood cooling system and chip pan.
Frequently Asked Questions (FAQs)
Let’s now look at the most often-asked questions about these apparatuses and other pertinent topics.
What Is a Bridgeport Knee Mill?
A “knee-and-column” machine with a rotating turret and sliding-ram top was created in 1936 by Rudolph Bannow’s firm.
The name stuck around on a shop floor for decades and was associated with sturdy, high-quality machine tools over the past eighty years.
Other machine makers have since cloned the idea, and Bridgeport no longer owns the business—Hardinge acquired it years ago.
Regardless of its true brand name, most machinists still refer to it as a Bridgeport (or, at the very least, a Bridgeport-type knee mill).
And although classic machines haven’t disappeared and don’t appear to be doing so any time soon, CNC machining centers have become the machining industry’s darlings—and rightfully so.
When Was the Knee Mill Invented?
It was developed by engineers Rudolph Bannow and business partner Magnus Walstrom in 1936.
After the city where they started producing and marketing their now-famous machine, they gave it the name Bridgeport.
Larger fish have subsequently devoured the Bridgeport Machine Company in the ocean of machine tools.
What Is a Fitz Machine?
The Fitz mill, also known as a comminuting mill, operates at high speed.
High-speed knives with impacting knives on one side and sharp knives on the other are used to shear the raw materials, crushing them.
You can choose from a variety of knives that we have available.
What Are the Types of Vertical Machines?
The two kinds of upright mills are bed mills and turret mills.
Why Do CNC Machines Utilize G Codes?
G instructions set up the machine to move in a specific manner. Typically, they come with coordinates so the machine can also know where to move.
To ensure that the CNC machine is operating in the appropriate mode, a few G commands are also used at the start of the program as “safety” settings.
Conclusion
We could go on, but to put it briefly, that’s it! I hope this guide helped you with your questions about these devices.
There is training to think about, just like any piece of machinery. Also, there is support, parts and service, and everything else, but you are already aware of it.
The majority of knee mills have 220-volt, 3-phase power. For businesses in industrial parks, where such power is typical, this is not a problem.
But you’ll need a phase converter to install a machine in a garage or outbuilding (preferably a rotary-style). A single-phase power supply could be a better option for your mill. That’s a good beginning!