Disclaimer: As an Amazon affiliate, I may earn a small percentage from qualifying purchases. This is at no extra cost to you. Learn more here.
If you are a budding machinist, you know how important it is to have an end mill to get things done on your workpieces, such as drilling holes or adding grip textures.
Yet, an end mill is not a one-size-fits-all deal because there are different types of end mills, and they are designed to carry out varied and specific workloads.
Today, I’ll be taking you through every nook and cranny of an end mill in this particular beginner’s guide. Read on!
KEY TAKEAWAYS:
- End mills are cutting tools that can help in milling processes such as plunge cutting, profiling, shaping, drilling, and V-grooving.
- There are different types of end mills, such as square end mills, bull nose end mills, flat end mills, and roughing end mills.
- End mills’ central bodies are either made with high-speed steel or solid carbide.
- End mills as cutting tools have protective layers on the outer surface, such as ARC evaporation, chemical vapor deposition, high-power impulse magnetron sputtering, and physical vapor deposition coatings.
What Does an End Mill Do?
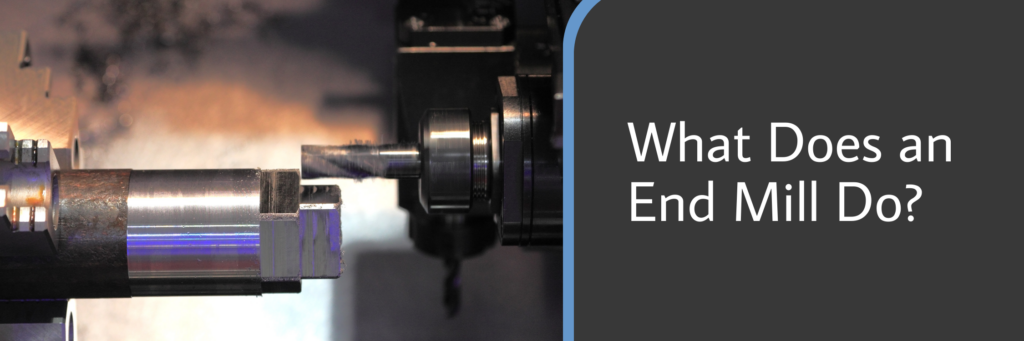
An end mill is a cutting tool, where its teeth are located at the peak and surrounding surfaces to cut through or plunge directly into workpieces to finish tasks, such as:
- Mill contouring surfaces
- Spotting
- Countersinking
- Material removal
- Cutting edges
- Face milling
Additionally, end mills are indispensable in different milling applications for the precise creation of a workpiece, and these are:
- Contouring or profiling of irregular surfaces to get the accurate design of a workpiece
- Counterboring to create a secured empty path for the screw to fit before it is actually used
- Drilling a solid surface before any complicated or complex milling process
For end mills to deliver these tasks as cutting tools for milling, it is crucial to check their structure as a top priority when choosing. This includes checking for:
- Stiffness
- Rigidity
- Chatter vibration
With the proper slender or broad design, end mills can be stable enough to create precise workpieces with lesser noise and vibration, ensuring longer tool life.
Different Types of End Mills
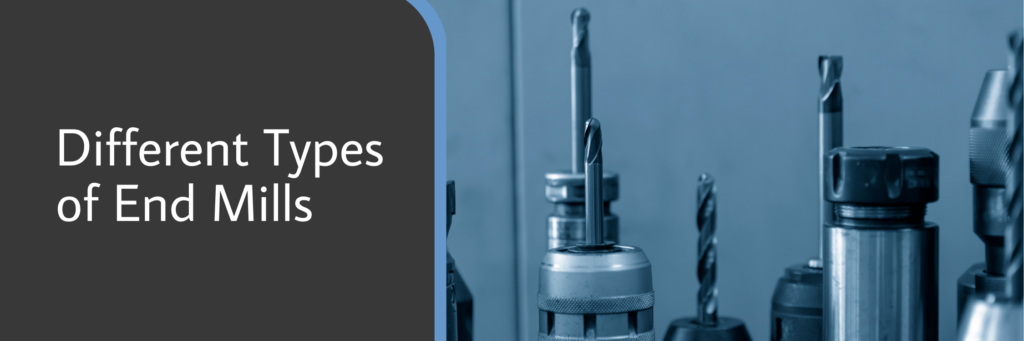
Different types of end mills vary in purpose, shape, size, and overall appearance. Here are the most common types of end mills:
- Ball nose end mill – A ball nose is used in a milling process that involves contoured surfaces, including 3-dimensional shapes.
The ball nose is characterized by a round cutting edge and a thick shank, usually with three flutes. It is also noticeable that the ball nose has an almost equal length of flute to the rest of the tool’s overall length. - Corner radius end mills – The corner radius end mills create a workpiece’s radius. These can also be utilized to blunt unnecessary sharp edges.
This tool is defined by its four flutes, with a shorter flute length and a longer overall tool length. - Double-end mill – This type has two ends, as its name suggests, which makes it more durable. With its four-flute feature on both short-flute sides, you can easily spot a double-end milling tool from afar.
- Finisher end mill – The finisher is characterized by one end with a square shape and a smooth diameter. It can help cut large objects and give them a smoother surface finish.
A good feature that sets the finisher from other end mills is that its flutes have ample space between them, making the tool pass through any workpiece with ease, allowing for a smooth finish. - Flat-end mills – Flat-end mills are designed for engraving and other rougher operations. These are also called the square end mills and are used for roughly anything under the milling process umbrella.
- Roughing end mills – When you want to remove a big chunk of material in one go, roughing end mills or hog mills can help you.
It has additional horizontal cutting tools on its cutting edge to work through heavy milling operations efficiently. But, it is also equally noticeable that its four-flute length is shorter than the overall length. - Solid carbide end mills – This type of end mill is made with premium materials, which ensure high-quality cutting and durability.
Solid carbide is one of the state-of-the-art materials when talking about a milling machine, milling cutters, end mills, and other similar sorts, as it is extremely heat-resistant and chip removal-resistant, especially when coated. - Undercutting end mill – Undercutting end mills or lollipop cutters are known for producing precise contours and profile workpieces.
You can quickly identify it as it looks like a lollipop. However, different models vary in terms of shank size, small angles, and surface feet per minute.
How to Choose An End Mill
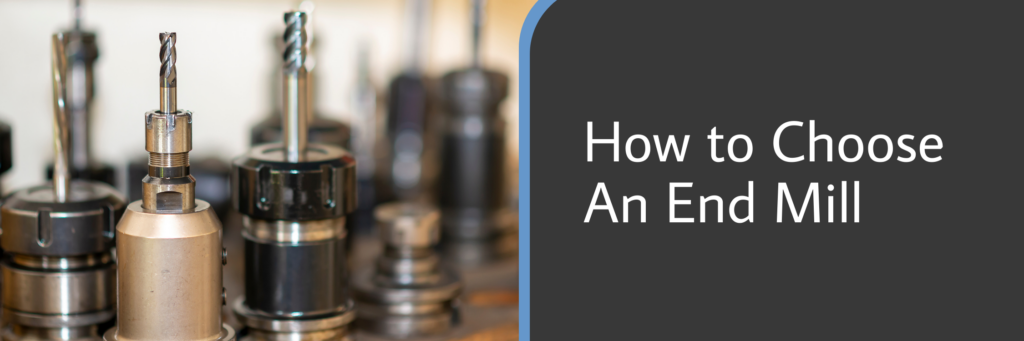
You cannot just pick an end mill you like and use it for a completely different workload. Before choosing an end mill, you need to consider certain factors explained in this section.
1. End mill coatings – Coated end mills are most likely to last longer because the coat stands as the protective layer between end mills and workpieces. It limits the direct impact on end mills, giving the former wear resistance.
Here are different kinds of coatings for your reference:
- Aluminum titanium nitride – This popular coating provides a thick coat that is highly resistant to heat and other environmental factors.
- Arc Evaporation – According to a study, arc evaporation is produced by electricity solidifying the end mills’ outer layer and adding thickness to their skin for more durability, even at higher temperatures.
More importantly, the cost of arc evaporation coating in a tool is rightfully set off by its above-standard performance when incorporated with a milling machine.
However, it may cause defects in quality in the long run if you are unaware of how to use and take care of it properly. - Chemical Vapor Deposition – The CVD coating is produced through different low to high-pressure processes to make thin films. As it is primarily thin, you will need multiple layers to achieve the desired thickness.
The thinness of a single layer of CVD coating can significantly influence how easy it is for milling cutters and end mills to chip off in shallow slotting, non-center cutting, and other machine tool tasks. - High-power impulse magnetron sputtering – The HiPIMS was discovered in the 1960s but only gained attention in 1999 and the years after because of its highly dense but smooth coating.
This is a high-technology approach to coating a square-end mill and others of different shapes because it can precisely cover even the nooks and crannies of a milling cutter. - Physical Vapor Deposition – The PVD film is made by vaporizing the substance at a high temperature and condensing it to form thin films designed to toughen the edge and strengthen the other part it coats.
However, choosing the physical vapor deposition will mean you must shell out a significant amount of money from your budget for the meager chance of having a premium tool.
2. End mill length – The length of end mills matter because the longer it is, the more secured it becomes as it lays flat on a collet.
With this, it can result in different benefits, such as:
- Minimize noise
- Lesser tool chipping
- Longer tool life
Moreover, there are two kinds of long-end mills: long-length end mills and long-reach end mills.
The long-length end mills have a longer flute, which is very efficient for deep-drilling holes, while the long-reach end mills have long flutes with smaller neck diameters.
3. End mill materials – To have a long-lasting cutting tool, it is essential to consider what the end mills are made of, such as hss vs carbide:
- High-speed steel – End mills made from HSS are budget-friendly, but the quality may quickly deteriorate with daily use.
- Tungsten carbide – If you frequently work with cast iron and other hard materials, tungsten carbide end mills are the best choice because they can perform longer under high heat and other factors.
4. Helix angle – The right choice of a helix angle will give end mills better performance, whether roughing end mills or finishing end mills.
To help you out, here is a list of the most used helix angles on the market:
- 35-degree angle – This angle is less aggressive when cutting but has higher strength which is fitting for roughing end mills.
- 40-degree angle – This angle lies in the middle with medium aggressiveness and strength, making it flexible and useable for a rough finish.
- 45-degree angle – This angle is the most aggressive of the three but has the most minor strength, making it a perfect fit for finishing the details of your workpiece.
5. Flute count – The flute count comes hand-in-hand with the helix when it comes to the number of spiral-shaped cutting edges of end mills. It is essential to consider because it determines an end mill’s finish, strength, and cutting depth.
The general rule for flute counts is that the more flutes there are, the greater the strength and the smoother the finish. On the other hand, the lower number of flutes means a better edge for a rough finish.
At the end of the day, it will still depend upon your preference and milling applications on whether to get end mills with fewer flutes or more flutes.
Frequently Asked Questions
I know you have some questions in mind regarding end mills and their usage. With that, I answered some of your FAQs in this section!
What is the Difference Between A Drill Bit vs. End Mill?
The difference between a drill bit and an end mill lies in their intended purpose. The drill bit is used to bore into a workpiece vertically, while the latter is used as a cutting tool that can be maneuvered sideways.
Aside from that main difference, here are other differences for your reference:
- Drill bits do not have cutting teeth as opposed to end mills
- Drill bits can have a single sharp center cutting end, while end mills have the meeting of flutes for the cutting end
- Drill bits’ center cuts in an axial direction to create holes while end mills move rotationally to perform center-cutting
Aside from giving you the differences, I also want to provide some of the things drill bits have that are also present in end mills:
- Drill bits are also made in high-speed steel and carbide
- Drill bits also have flutes
When Should You Use An End Mill?
You can use end mills for various projects, including the following milling operations:
- Shaping every irregular, curved, and flat surface
- Drilling round holes and narrow cuts
- Side cutting or non-center cutting of edges and sides
- Making rounded corners
- Face milling
- Plunge cutting (square-end mills)
- Precision cutting for sign-making, mold-making, and circuit boards
Final Thoughts
Now that you know what end mills are and what their existence entails, your milling process will surely be more efficient than usual.
Remember that end mills are effective cutting tools, depending on the milling applications (smooth or rough surface finish), provided you consider the following:
- Best end mills’ coatings
- Most appropriate length, materials, and helix angle
- The right number of flutes
So, what are you waiting for? Get one of the best home milling machines and start your milling process!